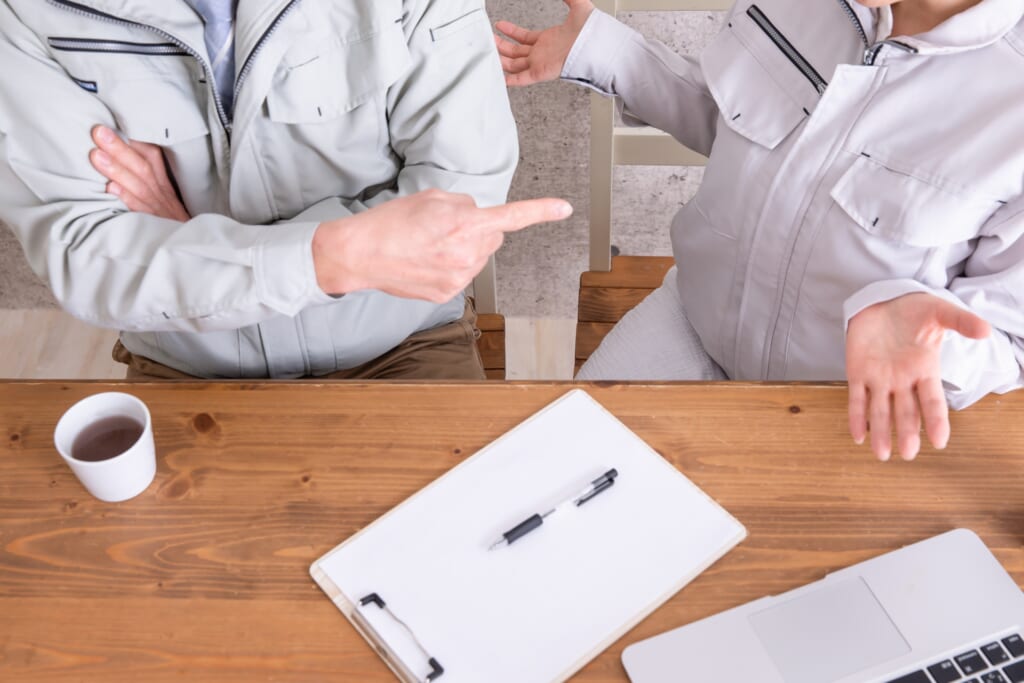
製造業で働いていると、一度はポカミスの対応に追われたことはありませんか。ポカミスさえなければさらに効率的に仕事ができたのにと思う場面も多いかと思います。
この記事では、ポカミスが起きてしまう原因からポカミスの予防・対策まで徹底解説します。ポカミスの対応に悩まれている方はぜひ参考にしてください。
弊社サンソウシステムズでは、導入社数No.1(富士キメラ総研 2023年8月8日発刊)国内トップシェアを誇る現場帳票システム「i-Reporter」の導入支援をおこなっています。
弊社では、導入を検討している方々が安心して導入していただけるように、導入前から課題のヒアリングをおこなっています。
現場のDXに悩みがある方は、サービス資料を用意しましたので、ぜひこの機会にこちらから無料でダウンロードしてみてください。
導入実績3,500社以上
目次
ポカミスとは
製造業におけるポカミスとは、主にヒューマンエラーによって起こるミスです。作業員の不注意や誤解により、不良品の発生や製造ラインの不稼働を招いてしまうことを指します。
人によるミスの場合、記認・認知・判断・行動の4つのポイントでミスを起こす可能性が高いです。これらはうっかりしていたミスが多いですが、手抜きやルールの無視といった意図的なミスも含まれます。人が起こすミスだからこそ、原因の見極めが大切です。
またポカミスの原因はさまざまで、作業環境・設備に問題があるケースも少なくありません。その場合、照度・騒音・温度・5Sの乱れなどが原因として挙げられます。
発生しやすいポカミス
作業中に起きるポカミスの中には、作業内で起きるものと作業員の怪我、納品の遅延などが挙げられます。
特にポカミスは作業内で発生しやすいため、一覧にして紹介します。
作業シーン | 具体例 |
受入 | 伝票や作業指示書の誤解 |
ピッキング | ピッキング中に部材を間違える、倉庫にあったゴミを混入させるなど |
設備オペレーション | 設備機器の操作、測定器からの計算を間違える工具や刃具のセット方法、設備機器で数値の調整を誤る |
組立作業 | 作業工程を飛ばす部品を間違えるネジを締め忘れる |
検査 | 不良品に気づかない |
梱包 | 捺印を忘れる付属品を間違えて入れる・入れ忘れる出荷先を間違える |
そのほか | 製品を落として、傷つけてしまう作業報告漏れ |
ポカミスの原因
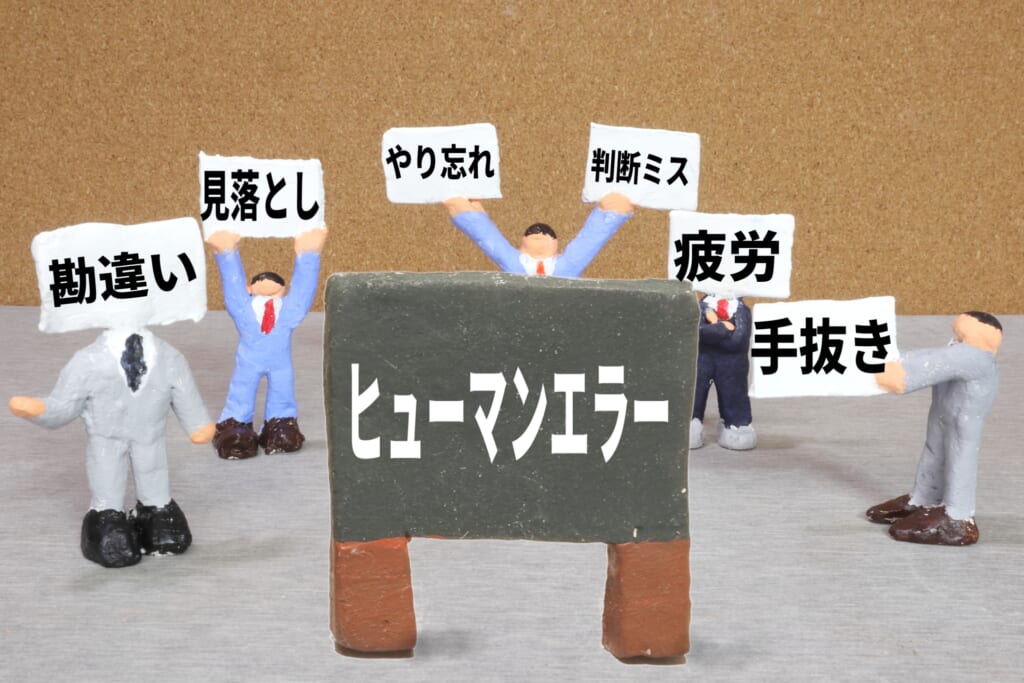
人が作業をおこなうことが多い作業現場ではどうしても起きてしまうのが、ポカミスです。ですが、内容によっては怪我や顧客からのクレームといった大きな問題に発展する場合もあります。
ポカミスの原因になりやすいポイントを抑えて、未然に防ぐ対策を準備しておきましょう。
ヒューマンエラー
ポカミスはヒューマンエラーの一部のミスを指します。ヒューマンエラーの定義は「意図しない結果を生じる人間の行為」であり、データ入力時の間違い、車のブレーキとアクセルの踏み間違いなどです。それに対して、ポカミスの定義は「不注意によるミスで、深刻な結果を引き起こす可能性があるもの」で、「うっかり」を含むミスです。
人が起こすポカミスの2つのタイプと4つの要因を紹介します。
タイプ | 要因 | 具体例 |
訓練で阻止可能なポカミス | 知識不足 | 手順を間違える工程の誤解 |
スキル不足 | ツールの間違った操作機械の操作ミス | |
モラル不足 | 手順を省く確認を怠る | |
阻止できないポカミス | ハード・ソフト系 | 機械の故障 |
作業環境や設備の問題
照度や騒音、温度などの作業環境や設備の問題は環境要因で、作業ミスにつながります。照度が暗すぎる場所では、部品の誤認や手順の見落としが発生しやすくなります。騒音が大きい作業環境では、指示の声や警告音が聞き取りづらくなる傾向が高いです。作業場の温度も寒すぎる・暑すぎると適温から大きく外れると作業員の集中力を低下させ、ミスにつながります。
また、作業スペースが整理整頓されていなかったり、機械の定期的なメンテナンスが実施されていなかったりすると、作業効率を低下させて、誤操作やミス・事故を引き起こします。
ルールや手順の不整備
作業員がルールや手順書の理解ができていない場合や、ルールや手順書自体が現場に適していない場合は作業ミスが発生しやすいです。曖昧な表現が多いマニュアルも、ミスを誘発してしまいます。
また、作業員がルールやマニュアルを守らないケースもあります。例えば、手順書でわからないまま作業を進めてしまったり、指定された部品ではない部品を使用してしまったりといったミスです。
作業員への指導不足
作業員に対して、十分な知識や指導がおこなわれないと、作業員は正しい判断ができません。作業と並行して新入社員のOJTをおこなうことは容易ではありませんが、教育を省いたり不十分だったりすると知識や技術は上がらず、ポカミスの原因になるため気を付けましょう。
ポカミスを防止する対策
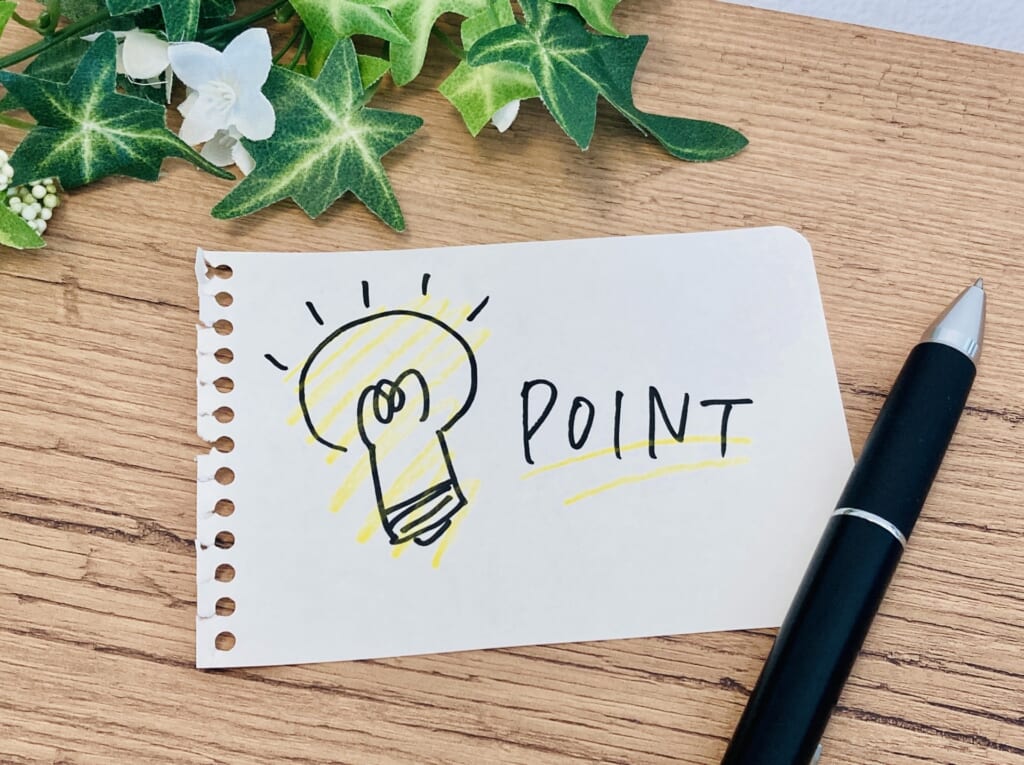
ポカミスの発生で会社は大きな損失を受ける可能性が高いです。ポカミスが起きてしまった際の対応手順や、どのような対応方法が最適かを紹介します。
人が作業をする上でポカミスを100%防ぐのは難しいですが、ポカミスのリスク軽減や起きてからの迅速な対応をすることが重要です。ぜひ参考にしてください。
原因を追求し、改善する
ポカミスが発生する理由が「ヒューマンエラー」「環境設備」「ルール」「教育」のどれが原因なのかを明確にします。原因の追求方法には下記のようなものが挙げられます。
分析方法 | 詳細 |
ルートコーズ分析※事象の原因を追求する方法 | 1)ポカミスが起きた具体的な事象を把握しますする 2)なぜ、どのように、いつ、どこで、誰が、何をしたかの5W1Hの質問で詳しく状況を整理する。 3)複数の原因を分析し、最もポカミスに影響を与えた原因を特定する。 |
フィッシュボーン図※ポカミスの原因を視覚的に整理する方法 | 1)ポカミスを中心に矢印を描く。 2)矢印から分岐させ、「人」「設備」「プロセス」「材料」などの要因を追記する。 3)各カテゴリーごとに具体的な要因を書き出していく。 |
そのほか、現場にいた作業員へインタビューやヒアリングをおこない、ヒューマンエラーが起きた原因を特定する方法もあります。
「なぜその手順を実行したのか」「どのような状況でミスが発生したのか」「作業環境はどのような状況だったか」などの質問が効果的です。
手順や工程のルールの見直し、マニュアルを整える
手順が複雑になるほど、ヒューマンエラーは起こりやすくなります。まずは「現在のマニュアルや工程に問題はないか」「誰が見てもわかるマニュアルになっているか」「いまの手順が最適かどうか」といった観点で手順や工程のルールを確認しましょう。
守るべきルールが間違っていた場合、ポカミスを防ぐことは難しいです。定期的な見直しがおすすめです。
作業員への指導を見直す
手順書やルールに問題がない場合、作業員の働き方や作業環境に注目しましょう。
作業をおこなう本人たちが「うっかり」ではなく「意図的に」ルールを守らない場合は、作業員への指導の見直しが重要です。また、作業環境が悪くクオリティを保って手順を進められない場合は、作業環境の改善が必要です。
日頃から作業員の「暑い」「暗い」「騒音がうるさい」といった声には注意しておくと良いでしょう。
システムの導入をして、作業量を減らす
ポカミスは人が起こすヒューマンエラーです。そのため、人が作業する業務を減らすのも方法の1つです。
作業員は、製造ラインを動かすだけでなく報告書や帳票管理といった事務処理もおこないます。製造ラインを変えることはできませんが、事務処理を電子化して作業員の負担は減らせるでしょう。
現場帳票を電子化する「i-Reporter」は、作業員の日報作成の日報作成・報告書作成を電子化ができます。
「i-Reporter」はシステム導入への疑問を解決する『ちょこっと相談室』という無料のオンライン相談窓口を設けております。ぜひ活用してみてください。
ポカミス対策例(ポカヨケ)
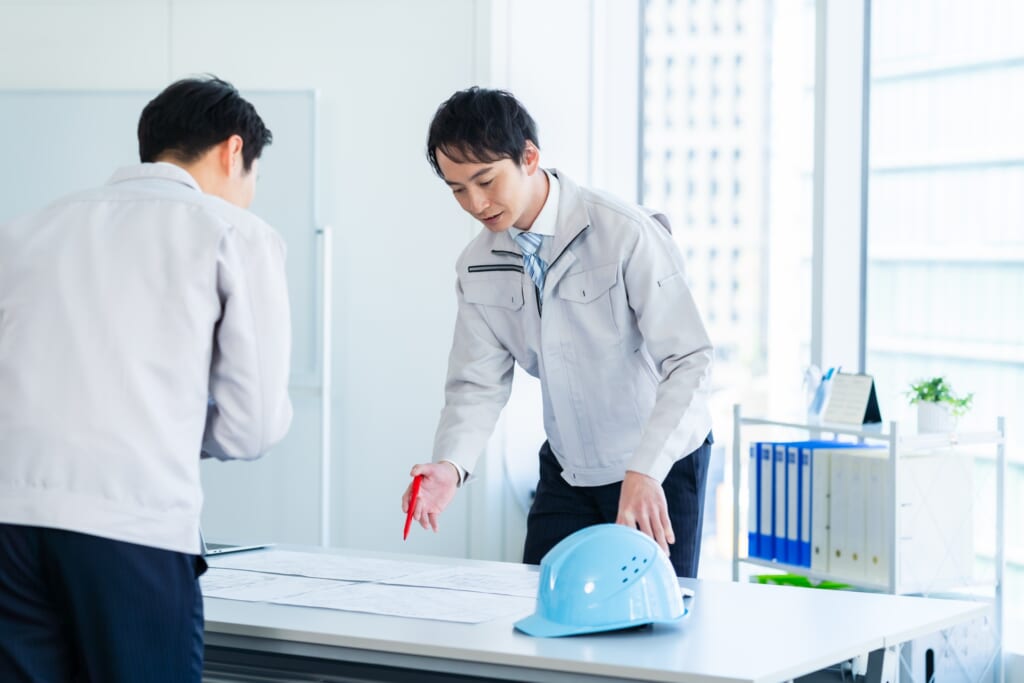
実際にポカミスの対策の事例をさらに具体的に紹介します。
すぐに現場に取り入れられるものもあるため、ぜひご検討ください。
設備や作業環境への投資
作業員の事務作業の自動化だけでなく、自動搬送ロボットや自動組立ラインの導入といったAIやIoTで作業員の手作業を減らせます。また、製造ラインに人が立ち入らないことで怪我のリスクの軽減が可能です。
作業環境への投資は金額が大きいものが多いです。しかし、ポカミスの発生頻度やポカミスの内容や原因と照らし合わせて最も改善が期待できる場合は、一度検討することをおすすめします。
KY活動を実施する
KY(危険予知活動)活動は、作業員同士が協力してポカミスを防ぐための活動です。ポカミスの原因につながりそうな場所や作業を洗い出して、事前にリスクの排除をおこないます。
手順は下記の通りです。
・現状把握:危険がどうかを見極め、洗い出す
・本質追求:重要な危険なポイントを捉える
・対策樹立:対策を検討する
・目標設定:作業員同士で行動目標を立てる
具体的な方法としては、「ヒヤリハット法則」や「危険を示すイラストや写真を使用する」などが挙げられます。また、指さし確認といったその場でできる方法も効果的です。
意識改革やルールの学習
作業員に対して定期的に教育やトレーニングをおこない、作業手順の理解度の向上と意識向上を目指します。方法として下記のものが挙げられます。
方法 | 詳細 |
OJT | 上司が部下に対して業務をしながら、必要なスキルや知識を教育する。 |
OFF-JT | 実際の作業現場ではなく、別の場所でおこなわれる教育。例)e-learningや集合型研修 |
e-learning | オンラインで教育やトレーニングをおこなう方法。作業員の好きな時間に学習ができる。 |
マニュアル作成 | 業務フローや留意点をまとめたマニュアルを活用する。 作業員の指さし確認やWチェックなどに貢献できる。 |
すべてを導入できなくても、現状取り入れられそうな方法を導入してポカミス対策を小さなポイントからでも早く始めることが重要です。
ポカミスを防いで、作業効率向上を目指す
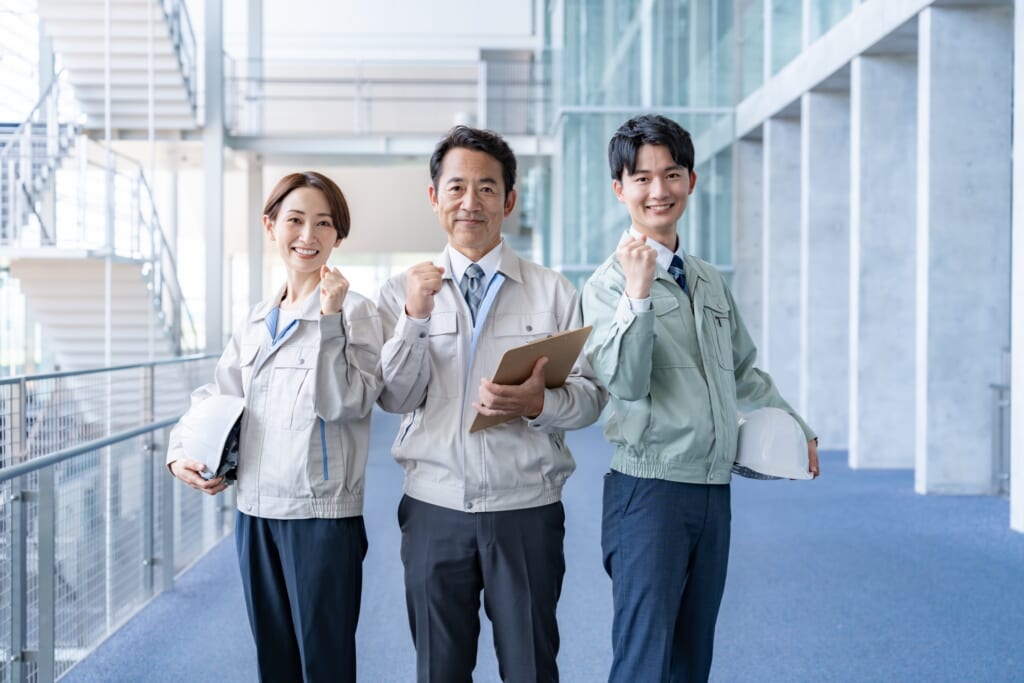
ポカミスは人が作業をしている以上、ゼロにすることは難しいですが、さまざまな工夫や取り組みをすることで減らせるミスです。
ポカミスの原因は些細なものでも、ポカミスによって発生した作業や損失を考えると、作業効率や作業員のモチベーションを著しく低下させる恐れもあります。
弊社サンソウシステムが運営している『ちょこっと相談室』という無料のオンライン相談窓口ではポカミスを防ぐための相談も受けつけています。
課題のヒアリングから最適な改善方法のご提案までお任せください。
少しでもAI導入やIoT化に興味がある方は『ちょこっと相談室』という無料のオンライン相談窓口にご相談ください。