工場の現場では、作業効率や品質、生産コスト、安全性など、さまざまな課題が常に存在します。これらの課題を解決し、競争力を高めるために欠かせないのが改善提案です。本記事では、工場改善提案の基本から、現場で役立つ具体的な改善アイデア、成功する進め方まで、わかりやすく網羅的に解説していきます。
「i-Reporter」は導入社数No.1(富士キメラ総研 2024年8月8日発刊)の国内トップシェアを誇る現場帳票システムです。
弊社株式会社サンソウシステムズでは、要件定義から設計・導入、その後の運用管理まで、お客様に寄り添った伴走支援が可能です。
ぜひ、ご一緒に現場の業務課題を整理していきましょう。サービス資料を用意しましたので、あわせてこの機会にこちらから無料でダウンロードしてみてください。
導入実績3,500社以上
目次
工場における改善提案の基本
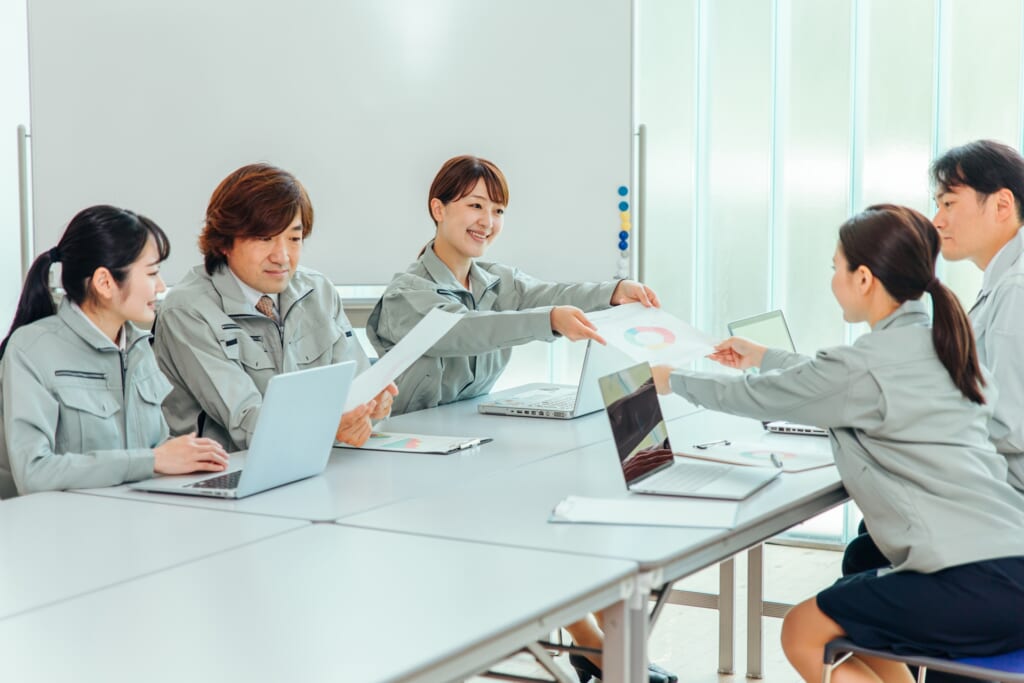
工場における改善提案は、生産性や品質向上に直結する重要な活動です。本章では、改善提案の基本的な考え方や目的、対象領域について詳しく解説します。
改善提案の考え方は、日本の製造業の発展とともに進化してきました。特にトヨタ生産方式ではカイゼンという概念が体系化され、現場主導の小さな改善が世界的にも高く評価されています。改善提案は、現場力向上の根幹を支える活動です。
なぜ今、工場の改善提案が重要視されているのか
少子高齢化、原材料価格の高騰、エネルギーコスト上昇、そしてグローバル競争の激化など、工場を取り巻く環境は年々厳しくなっています。加えて、カーボンニュートラルやSDGs対応など、企業には社会的責任を果たすことも求められるように変化しています。
このような背景から、トップダウン型ではなく、現場からボトムアップで課題を拾い、すばやく改善していく文化づくりが不可欠です。
改善提案活動を強化することは、コスト競争力だけでなく、企業の持続的成長を支える重要な戦略です。
改善提案の効果
工場における改善提案の主な目的と期待される効果は、以下の通りです。
- 作業効率向上による生産性アップ
- 品質改善による顧客満足度向上
- コスト削減による収益力強化
- 職場の安全性向上による事故防止
- 従業員のやりがい向上と定着率向上
特に近年は、従業員エンゲージメントを高める手段としても、改善提案活動が注目されています。
どのような領域が改善対象なのか
改善対象となる領域は広範囲に及び、具体的には以下のような領域が挙げられます。
領域 | 詳細 |
作業方法の最適化 | 手順の簡素化 |
設備の稼働率向上 | 故障予防 |
工程設計の見直し | ボトルネック排除 |
材料・在庫管理 | 過剰在庫削減 |
安全衛生対策 | 危険エリアの明示 |
エネルギー管理 | 待機電力削減 |
このように、工場内のあらゆる領域が、改善提案の対象になり得ます。
改善提案制度とは?導入企業の事例紹介
改善提案制度とは、従業員からの改善アイデアを公式に募り、評価・実施・表彰する制度です。
導入事例として有名なのが、トヨタ自動車の改善提案制度です。現場から上がる年間数十万件もの提案が現場力を支えています。
他にも、オムロンや日産など、国内有数の製造業が積極的に導入しており、改善提案数と企業競争力には相関があるといわれています。
よくある工場の課題と改善提案の方向性
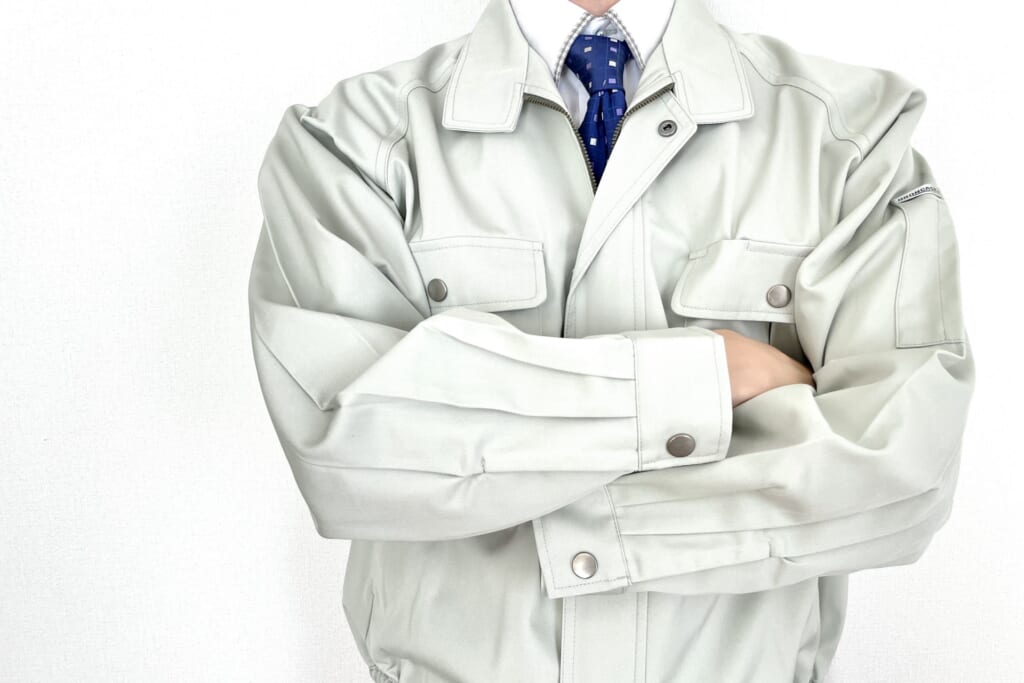
工場改善を進めるためには、まず現場で直面している課題を正しく把握することが大切です。本章では、代表的な課題と、それぞれに対する改善提案の方向性について紹介します。
なお、工場における課題が見逃されやすい背景には、現場の慣れがあります。長年続く作業手順や設備配置は、問題点を当たり前と認識してしまう要因です。課題発見の第一歩は、既存のやり方を疑う視点を持つことから始まります。
作業効率の問題
工場現場で最も頻繁に発生する課題が、作業効率の低下です。例えば、作業者が頻繁に道具を探す場合や、無駄な移動が多いと、生産性が大きく下がります。
これらのムダは、現場を丁寧に観察することで必ず見つかります。作業台のレイアウト変更や、部品・工具の定位置管理、作業手順の見直しなど、小さな改善から取り組むことが重要です。
品質不良の削減
品質不良は、手直しコストや返品対応、顧客満足度低下といった大きな損失をもたらします。不良品を減らすためには、不良が発生した理由を徹底的に追究する姿勢が求められます。
例えば、作業ミスを減らすために『ポカヨケ(ミス防止策)』を導入することや検査工程を標準化するなどの工夫が有効です。
コスト削減
原材料価格の高騰やエネルギーコスト増加に直面する中、コスト削減は企業存続に直結します。
例えば、資材ロスを削減するための標準作業書作成、省エネ設備の導入、ジャストインタイム方式での在庫管理などが代表例です。
単なるコストカットではなく、無駄の根本原因へのアプローチこそが工場改善提案では求められます。
安全性向上
安全対策は、作業者の命を守るだけでなく、企業の社会的信用を守る意味でも極めて重要です。
改善提案活動においても、ヒヤリハット事例の収集と改善、リスクアセスメントに基づく対策立案、5S活動の徹底などが不可欠です。
安全性向上は、労災発生率の低下、保険料率の改善にも直結します。
成果が出る改善案アイデア集
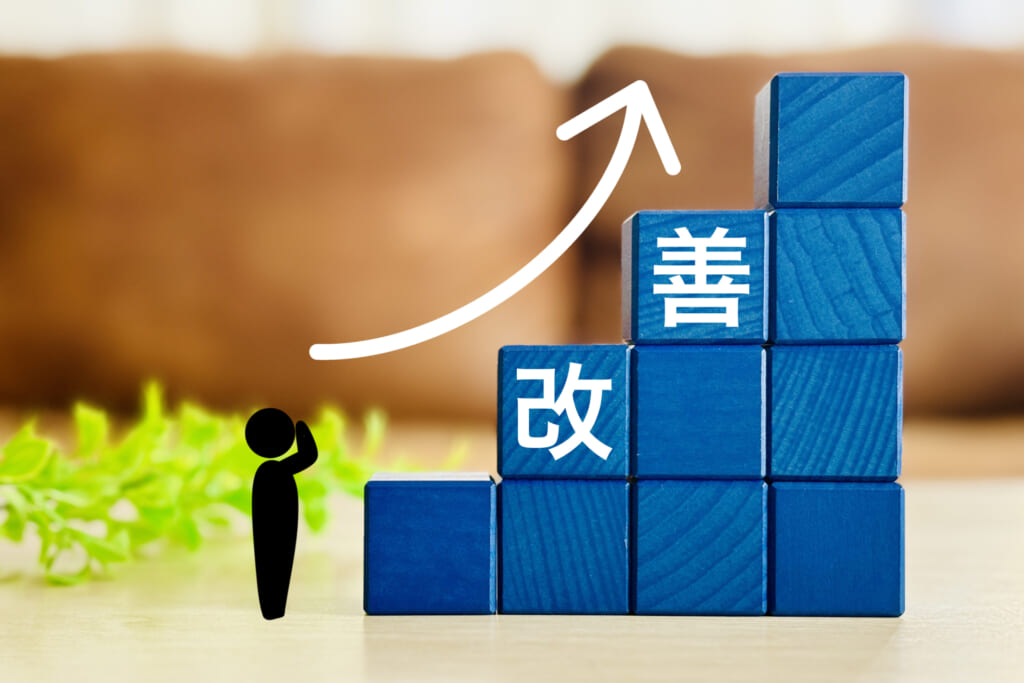
実際に成果を上げるためには、具体的な改善アイデアが必要です。本章では、作業改善・設備改善の両面から、現場ですぐに活かせる具体例を紹介します。
改善案を実施する際には、必ず小さな試験導入(トライアル運用)をおこなうことが大切です。いきなり全体に適用するのではなく、限定エリアで試行し、効果と副作用を見極めましょう。慎重な導入と現場フィードバックを繰り返すことで、失敗リスクを抑えながら確実に成果を上げることができます。
作業改善アイデア
作業面を改善するためのアイデアは下記のとおりです。現在の課題とほしい成果を照らし合わせて参考にしてください。
改善内容 | 成果 |
作業台の高さ調整 | 作業者の体格に合わせることで、疲労軽減と作業スピード向上を実現。 |
工具の定位置管理 | 定位置管理で探す時間をゼロにし、1日あたりの時間短縮に成功。 |
作業手順の標準化 | 作業マニュアル整備で新人教育の時間を削減。 |
作業動線の見直し | レイアウト変更で作業距離を短縮。 |
設備改善アイデア
作業面を改善するためのアイデアは下記のとおりです。
改善内容 | 成果 |
設備の定期点検 | 月1回の点検で年間故障件数を削減。 |
予防保全の導入 | センサー導入による異常検知で、突発故障ゼロ達成。 |
設備の稼働状況の可視化 | IoT活用でリアルタイム稼働監視、稼働率を向上。 |
設備のエネルギー効率化 | インバータ制御導入で電力使用量削減。 |
環境対策
近年では、環境負荷低減への対応も必須課題となっています。
工場改善提案の中でも、省エネルギー活動、廃棄物削減、リサイクル推進といったテーマが重要視されています。
例えば、LED照明への切り替えや、排水処理プロセスの見直しなど、小さな取り組みでも大きな効果を生む可能性があります。
現場が動く!改善提案の進め方
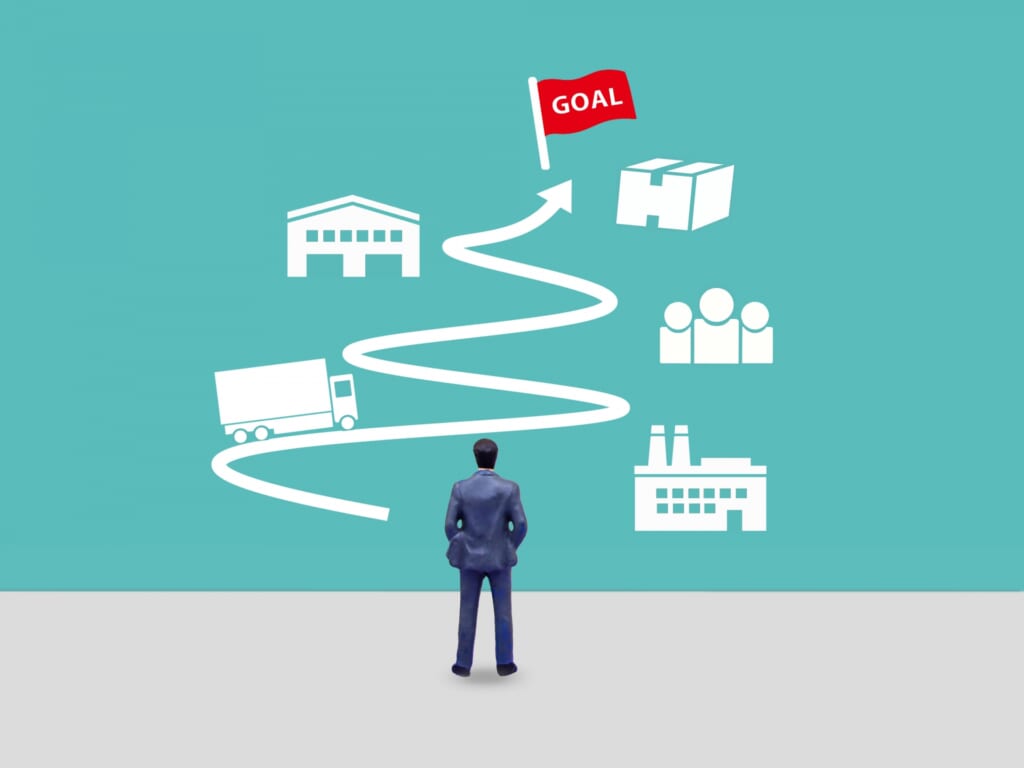
改善提案活動を軌道に乗せるためには、進め方に工夫が必要です。本章では、提案活動を成功させるためのコツや、評価・定着のための仕組みづくりについて解説します。
例えば、月1回の改善発表会を導入したところ、現場の提案数が3倍に増加した例があります。成果をチーム全体で共有し、感謝の言葉をかけ合う文化を作ったことが、改善提案の自走化につながった事例です。こうした工夫が、現場のモチベーションを維持する秘訣です。
改善提案活動を成功させるコツ
改善提案活動を効果的に進めるためには、現場任せにするだけでは不十分です。誰もが参加しやすく、成果が見える仕組みを作ることで、継続的な改善サイクルが生まれます。ここでは改善活動を現場に定着させ、モチベーションを高めながら運用するための実践的なコツを紹介します。小さな成功体験の積み重ねが、やがて工場全体の競争力強化につながるはずです。
小さな改善から始める
すぐできることや自分たちで実現できる改善から始めることで、活動のハードルを下げ、成功体験を積み上げやすくなります。
例えば、清掃用具の置き場所を見直す改善やチェックリストを作るなどです。
全員参加を促す仕組み作り
提案制度を作っても、一部の人しか出さないのでは意味がありません。
全員参加を促すためには、提案のハードルを下げ、フィードバックを迅速に返すことがポイントです。
成果を見える化する
改善前・改善後の数値や写真を掲示板や社内ポータルに掲載し、成功事例を全社で共有しましょう。改善提案すればこんなに成果が出るという実感が、次の提案を生み出します。
改善提案の評価と表彰制度の作り方
- 定期的に改善提案コンテストを開催
- 優秀提案者には賞金・表彰・社内報での紹介
- 部署単位での提案件数・実施率ランキング公表
これにより、モチベーションを維持しながら提案数を増やすことができます。
また、評価基準は「実施のしやすさ」「影響範囲」「費用対効果」「創造性」といった複数軸で設けることで、さまざまなタイプの提案を公平に評価できる仕組みになります。さらに、過去の受賞者にミニインタビューを行い、社内ポータルで掲載するなど、「提案の見える化」や「成功事例の共有」を通して、参加者のロールモデルを提示することも有効です。
改善が定着するチーム作り
リーダーシップのあるチームリーダーが、改善提案活動の旗振り役になることが重要です。
また、定例の改善ミーティングを設け、継続的にPDCAを回しましょう。加えて、チーム全体に改善マインドを根付かせるためには、日常業務の中に気づきメモや改善ノートなどの記録ツールを取り入れることも有効です。ちょっとした気づきを可視化することで、提案の種が集まりやすくなり、チーム全体が改善目線で現場を捉える習慣づけにつながります。
また、リーダー自身が改善提案を積極的に実践・共有することで、行動で示すリーダーシップがチームに良い影響を与えます。単なる管理者ではなく現場の応援者としての姿勢を示すことが、提案文化の定着には欠かせません。
注意する改善提案とその回避策
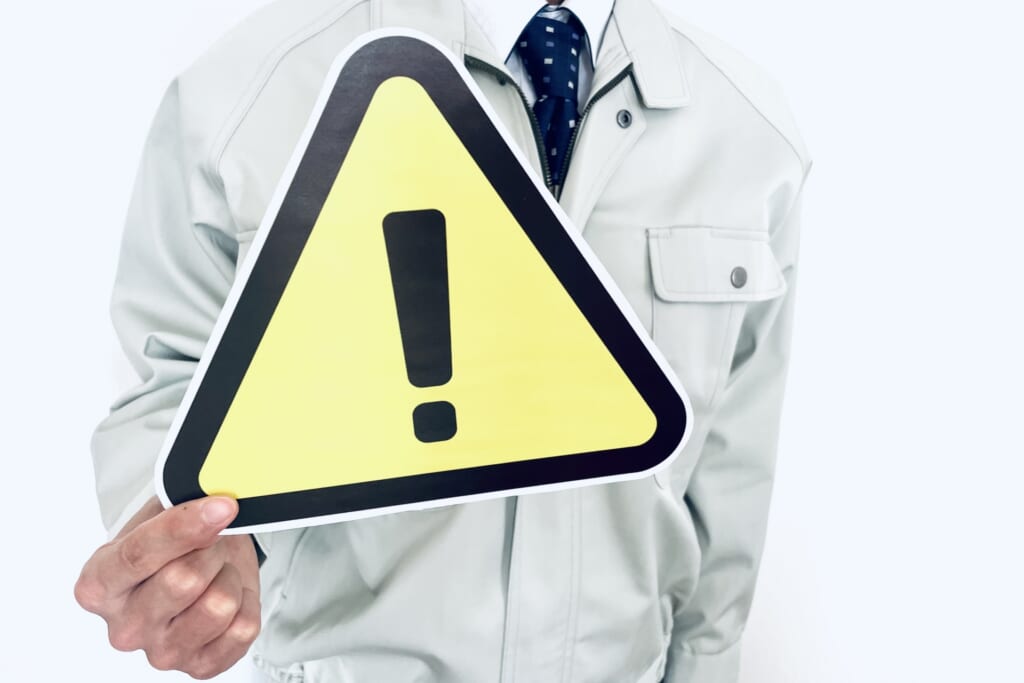
改善提案活動は、進め方を間違えると形骸化してしまうリスクもあります。本章では、よくある失敗パターンと、それを未然に防ぐための注意点を整理します。
失敗を防ぐためには、現場実態をしっかりと把握した上で、机上の空論に陥らない提案活動を心がけることが必要です。
よくある失敗パターン
どれほど優れた仕組みや制度があっても、改善提案活動は運用次第で形骸化してしまう恐れがあります。特に、現場との温度差や目的の共有不足が原因で、活動そのものが形だけになってしまうケースは少なくありません。ここでは、実際の現場でよく見られる失敗パターンを基に、陥りがちな落とし穴とその回避策を詳しく解説します。
現場が見えていない机上の空論
改善提案をおこなう際に、現場の実態を十分に把握せずに立案すると、絵に描いた餅になりかねません。
例えば、設備の自動化提案をしたものの、実際はスペースが足りず設置できなかった、というケースが挙げられます。現場観察、作業者へのヒアリング、試行導入など、現実をしっかり踏まえた上で提案することが大切です。
成果が数値化できない
改善効果を「何となく良くなった気がする」だけで済ませてしまうと、次の改善提案の説得力がなくなります。
例えば、作業時間削減なら1工程あたり15秒短縮、1日あたり○分の短縮と具体的に定量化が重要です。数値化によって、関係者全員が改善の成果を実感できるようにしましょう。
失敗を防ぐために必要なこと
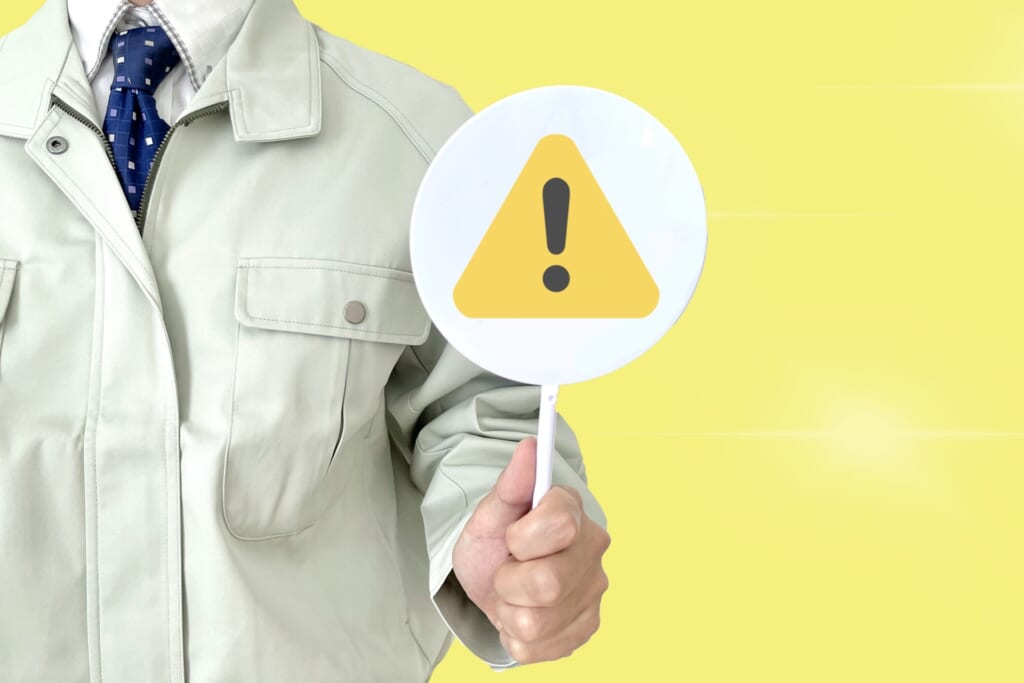
改善提案活動を継続的に成功させるためには、いくつかの重要なポイントを押さえる必要があります。本章では、失敗を防ぎ、成果を最大化するための具体策を紹介します。
工場での改善提案活動を定着・成功させるために、以下のポイントが重要です。
ポイント | 詳細 |
目的意識を共有する | なぜ改善提案をおこなうのか、活動の意義を全員に周知する。 |
KPI(重要指標)を設定する | 提案件数、実施率、コスト削減額などを指標として可視化する。 |
小さな成果を積み上げる | いきなり大きな成果を求めず、小さな成功を積み重ねる。 |
継続的な教育をおこなう | 改善提案力を高めるため、5S研修、QC研修などを定期的に実施。 |
成果を称賛・共有する | 成功事例は必ず社内で共有し、提案者を称賛する。 |
これらを意識して取り組むことで、工場改善提案活動の失敗リスクを大幅に低減できます。
過去の失敗事例として、評価基準が不透明なため、提案者のモチベーションが下がったというケースがあります。この反省から、提案内容の効果だけでなく、提案した行動自体を評価する方式に切り替えた企業では、再び提案活動が活性化しています。継続的な改善活動は、現場力だけでなく、従業員満足度や企業ブランド力向上にも寄与します。
これからの工場に求められる改善提案とは
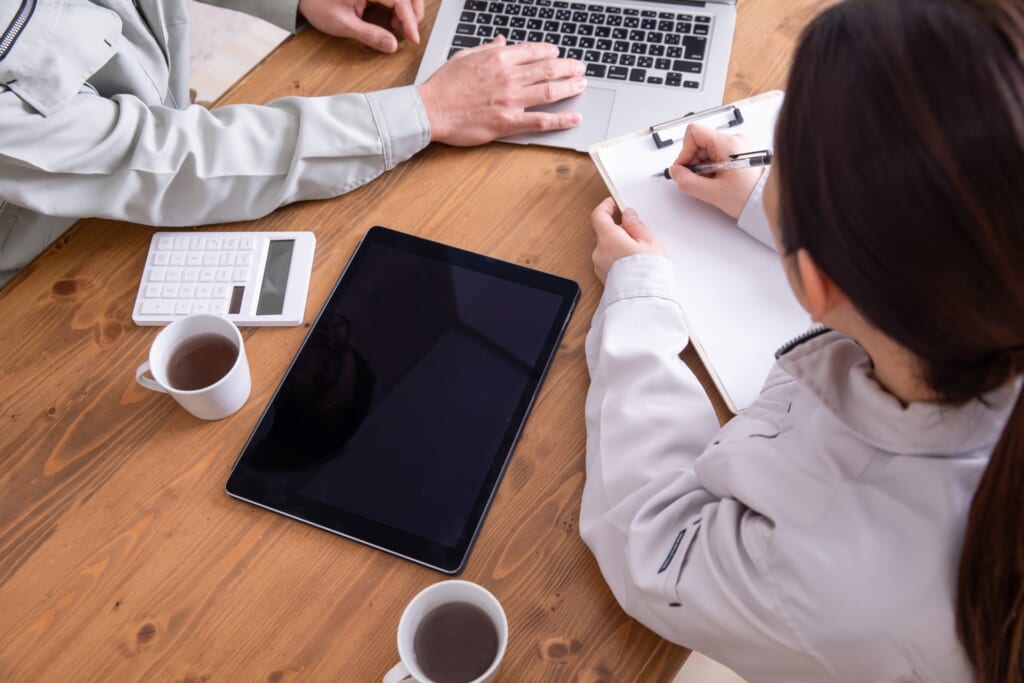
時代とともに工場運営に求められる改善の方向性も変化しています。本章では、デジタル化やSDGsへの対応、多様性に配慮した改善提案の重要性について解説します。
特に、スマートファクトリー化に取り組む際は、システム導入=改善完了と考えないことが重要です。IoTやAIを取り入れるだけでは不十分であり、現場運用に合わせたすり合わせや、常にフィードバックを受けながら最適化を続ける姿勢が求められます。
デジタル化・スマートファクトリーへの対応
今後の工場は、IoT・ビッグデータ・AIを活用した『スマートファクトリー化』がますます進んでいきます。
改善提案も、IoTセンサーで不良傾向を検知する、設備データから最適な保守時期を予測するなどといった、デジタル活用を前提とした内容が求められます。
現場のデジタルスキル向上も、今後の重要テーマです。
SDGs・環境配慮型工場の推進
持続可能な社会を目指すため、工場もCO₂削減、リサイクル促進、省エネ活動に積極的に取り組む必要があります。
工場改善提案においても、環境負荷を下げるにはどうするか、廃棄物をどう減らせるか、といった視点を取り入れることが、企業の競争力向上につながります。
多様性と働きやすさを考慮した改善提案
女性、高齢者、外国人労働者など、多様な人材が働く現場では、誰にとっても働きやすい環境づくりが不可欠です。
例えば、力の要らないアシスト機器導入、わかりやすいマルチ言語マニュアル作成など、多様性に配慮した改善提案が今後ますます重視されていきます。
工場改善に必要な要素と実践
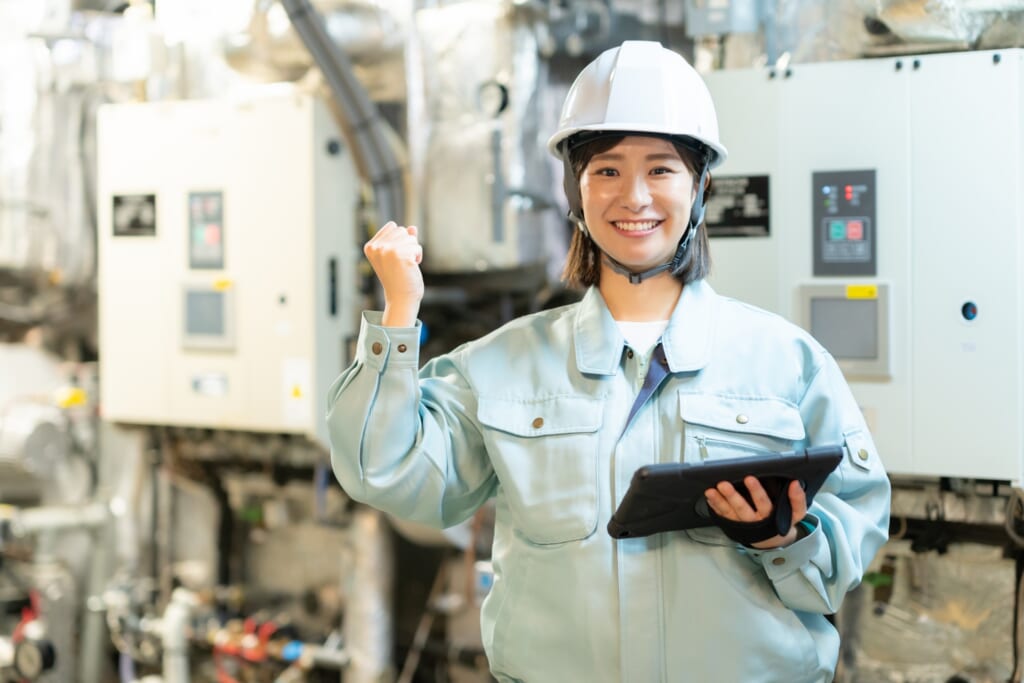
工場の改善活動を持続的に成功させるには、観察力、チャレンジ精神、全員参加意識、効果の数値化、社会・環境への配慮が不可欠です。さらにこれらを効率的に支援するデジタルツール活用も重要です。小さな気づきから始めることが、大きな変革の第一歩です。今すぐ現場を見渡し、できることから一歩踏み出してみましょう。改善提案は未来の競争力を生み出す武器へとつながります。
例えば「i-Reporter」は、現場帳票のデジタル管理を可能にし、作業記録の工数を削減し、データ紛失リスクを防ぎます。また導入から運用まで伴走支援が可能なため、導入して終わりという状態を防ぎます。
弊社サンソウシステムズでは「i-Reporter」の導入支援をおこなう無料相談窓口『ちょこっと相談室』を設け、導入前に課題ヒアリングから導入・運用までのシミュレーションが可能です。工場改善に悩む方は、ぜひご活用ください。