近年、製造業の現場では、原材料費の高騰や人材不足などの要因により、無駄をなくし効率良く働くことが求められています。無駄をなくしたいと考えていても、どのような方法で効率化を進めていけば良いのか悩む場合も多いのではないでしょうか。
生産工程の無駄をなくし利益を最大化する方法の一つにTPM活動があります。この記事では、TPM活動の基本から最新の進め方まで詳しく解説します。自社の生産におけるロスを削減したいと考えている方はぜひ参考にしてください。
「i-Reporter」は導入社数No.1(富士キメラ総研 2024年8月8日発刊)、国内トップシェアを誇る現場帳票システムです。
導入することで、紙の現場帳票の「記入・報告・管理」すべてのペーパーレス化を実現し、さまざまな業務の効率化やDXにつなげられます。
また、弊社株式会社サンソウシステムズでは、要件定義から設計・導入、その後の運用管理まで、お客様に寄り添った伴走支援が可能です。
ぜひ、ご一緒に現場の業務課題を整理していきましょう。サービス資料を用意しましたので、併せてこの機会にこちらから無料でダウンロードしてみてください。
導入実績3,500社以上
目次
製造業の無駄を削減するTPM活動とは
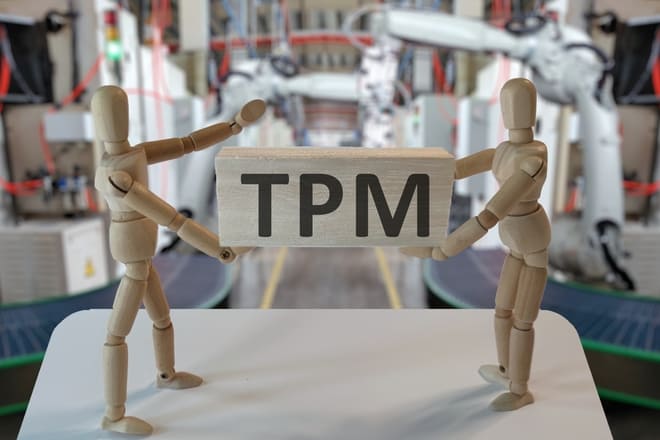
TPMとは、Total Productive Maintenanceの頭文字を取ったもので、直訳すると全員参加の生産保全のことです。他に、全員参加の生産マネジメント(Total Production Management)の頭文字と言われることもあります。
1971年に公益社団法人日本プラントメンテナンス協会と日本電装株式会社(現:株式会社デンソー)が、従業員全員が取り組む保全活動を共同で開発した取り組みがベースとなっています。TPM活動は、日本だけではなく世界中の会社で取り入れられ広がっている活動です。
TPM活動の目的
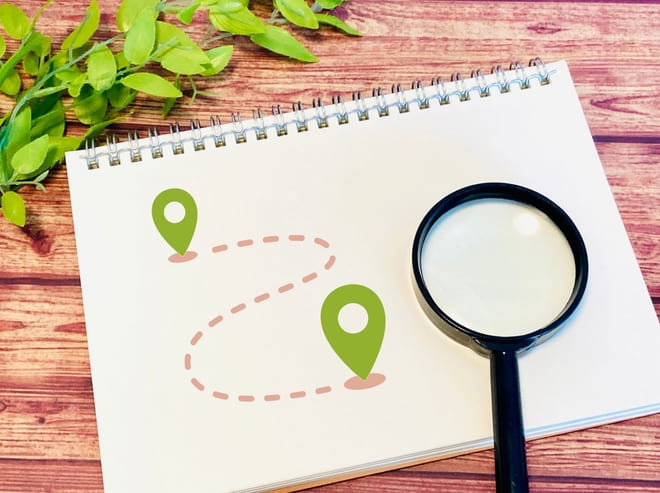
TPM活動の最大の目的は、あらゆるロスをなくすことです。製造業の生産プロセスにおけるすべてのロスを把握しゼロを目指すことで、企業利益の最大化に貢献します。
TPM活動をおこなう際、具体的には以下の3つを意識することが重要です。
- 生産システムを最大効率化する
- 災害・不良・故障ゼロを目指しロスをなくす
- 現場の従業員から経営の管理部門まで全員が取り組む
TPM活動が最大化すると、全員が参加してより良い製造業の現場が作り上げられます。
TPM活動の16大ロス
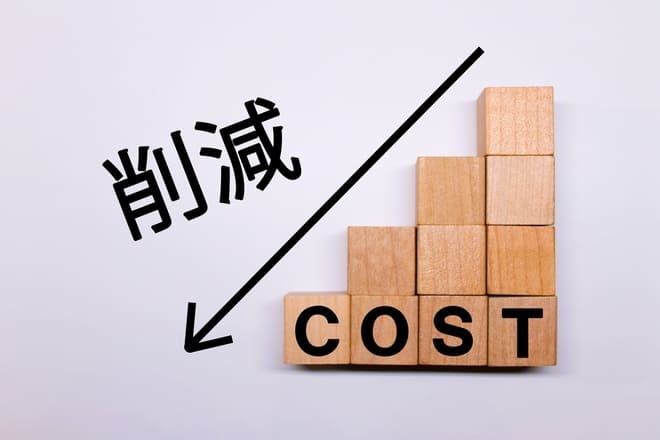
TPM活動では、生産プロセスのあらゆるロスを把握することが重要です。生産プロセスにおけるロスは、設備・人・原単価の3つに区分され16大ロスとして定義されています。ここからは、TPM活動で把握すべき16大ロスについて、それぞれ解説します。
設備効率を阻害する8大ロス
設備効率を阻害するロスは、時間を基準として捉えられます。設備で使用される機械が万全の状態で良品を生産できる時間と、現状かかっている時間を差し引きした分が設備効率を阻害するロスとなります。TPM活動で設備効率を阻害するロスは、要因別に8つ定義されています。
設備のロス | 詳細 |
---|---|
故障ロス | 設備の故障による生産停止 |
段取り・調整ロス | 生産切り替え時の調整時間 |
刃具交換ロス | 刃具の交換や調整にかかる時間 |
立ち上がりロス | 設備の稼働開始時の不安定な状態 |
チョコ停・空転ロス | 短時間の停止や無駄な動作 |
速度低下ロス | 設備の設計速度よりも低速での稼働 |
手直し・不良ロス | 不良品の発生や修正作業 |
シャットダウン(SD)ロス | 計画的な設備停止によるロス |
万全な状態と現状に差がある場合には、上記の表に記載されたロス要因がないか確認し、それぞれ対策を立てていく必要があります。
人の効率化を阻害する5大ロス
人の効率化を阻害するロスは、工数を基準として捉えられます。本来の理想とする工数に対し、現状の工数を比較して差し引きする必要があります。TPM活動では、人の効率化を阻害するロスは以下の5つが要因として定義されています。
人のロス | 詳細 |
---|---|
管理ロス | 材料待ちや指示待ちなどの管理上のロス |
動作ロス | 作業方法やスキルの差による無駄な動作 |
編成ロス | ラインバランスの不均衡による手待ち時間 |
自動化置換ロス | 自動化できる作業を手作業でおこなうことによるロス |
測定調整ロス | 品質管理のための頻繁な測定や調整 |
それぞれの要因が発生している理由を突き止め、改善を計ればロスの削減が可能です。
原単価の効率化を阻害する3大ロス
原単価のロスは、費用を基準として捉えられます。理想の材料費と現状の出荷時にかかる材料費を比較し、余分な費用がかかっていないか確認します。TPM活動では、原単価の効率化を阻害するロスは以下の3つが要因が考えられるとしています。
原単価のロス | 詳細 |
---|---|
歩留まりロス | 原材料の使用効率の低下 |
エネルギーロス | 電力や燃料などのエネルギーの無駄 |
型・治具ロス | 製品製造に必要な型や治具の製作・補修によるロス |
原単価のロスは、費用で比較できない場合には重量を基準とすることも可能です。原材料のロスを減らせば、利益の拡大が見込めます。
TPM活動の8本柱
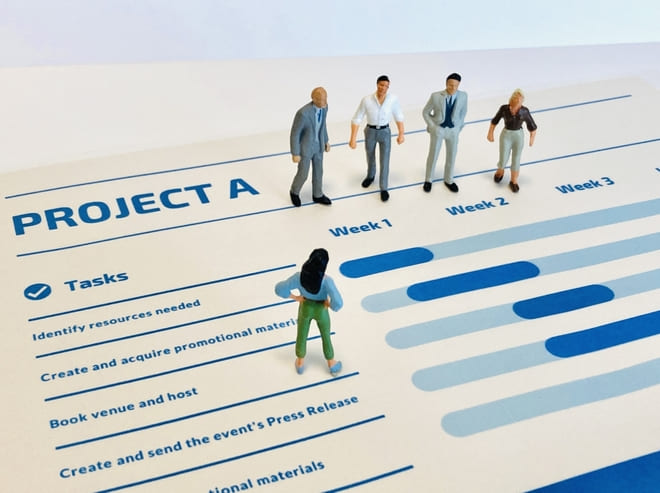
TPM活動は、管理部門を含めた社員全員で取り組むことが重要です。生産に関わる部門や機能ごとにチームを作り、ロス削減に向けた取り組みをおこないます。チームによる小集団活動のことをTPM活動では柱と呼び、機能別に以下の8つが定義されています。
8つの柱 | 詳細 |
---|---|
個別改善 | 生産ラインの各工程や設備を個別にチェックし、問題箇所を改善する活動 |
自主保全 | 作業者が設備の点検・清掃・潤滑を行い、故障を未然に防ぐ活動 |
計画保全 | 設備の寿命を延ばし、突発的な故障を防ぐための計画的なメンテナンス |
品質保全 | 不良品の発生を防ぐために、設備や工程の品質管理を徹底する活動 |
教育・訓練 | 作業者のスキル向上を目的とした教育・訓練の実施 |
安全・衛生・環境 | 労働環境の改善を通じて、安全で快適な職場を作る活動 |
設備初期管理 | 新規設備の導入時に、最適な運用を確立するための管理活動 |
管理・間接 | 生産現場だけでなく、管理部門も含めた全体的な改善活動 |
各チームは職場のルールや環境の改善を通じて、維持管理ができるよう責任を持って取り組むことが重要です。職場が抱えるさまざまな課題や不具合をチームのメンバーだけで解決を目指すのではなく、関係部門や管理者と連携し職場全体のレベルアップを目指します。
TPM活動の基本ステップ
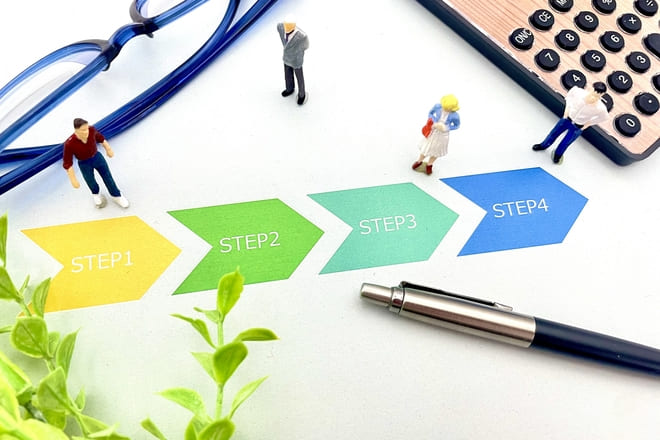
TPM活動を各チームで進めていくためには、どのようなステップを踏めば良いでしょうか。対処するロスによって原因や対策は異なっても、活動を進めていく流れは共通しています。ここからは、TPM活動の基本ステップについて解説します。
1.改善のテーマや目標を決める
TPM活動を始めるには、現状の分析をし、テーマや目標、役割分担を決めます。まずは目標のコストを定め、現状のコストと比較し、解決すべき課題の難易度・費用・改善効果の大きさから優先順位を決めることが重要です。
改善効果が高くとも費用や難易度の高いものは、一旦見送るという判断も必要となるでしょう。会社の状況に合わせて優先順位をつけることがポイントです。優先順位の高いものから改善を担当するチームへ割り付けます。
2.改善する計画を立てる
テーマや目標が決定したら実際に改善をする計画を立てます。ロスに対して実施する内容を決め、担当するチームのスキルに合わせて分担します。チームに所属する社員のスキルがアップする内容にすることが理想的です。
ここでいうスキルとは、品質管理(QC)で用いるパレート図を使いロス分析ができるようになることを指します。製造業における品質管理については、下記の記事で詳しく解説していますので、参考にしてください。
https://www.satfaq.jp/dx-column/factory-quality-control/
なお計画を立てる際には、進捗管理がしやすいようなるべく日程計画までしっかり立てることがおすすめです。
3.原因を解析し対策を考える
計画が完成したら、次は現状の分析をおこない、ロスを引き起こしている原因を解析し対策を考えます。必要に応じて動画で記録を残し、検証することが重要です。原因の分析には、特性要因図やなぜなぜ分析、PM分析などさまざまな手法を活用します。
原因が特定できたら、どのような対策をとれば対処できるか実現できるものを考えます。
4.実際に改善をおこなう
改善計画に基づいたスケジュールで、改善策を実行に移す段階です。場合によっては、事前に予算の申請、関係者への周知をしなければなりません。改善計画を実行する上で、安全対策も欠かせない要素です。計画した改善案を実行するにあたり危険な箇所はないか、事前に確認しておきます。
5.改善の効果を確認する
改善計画を一通り実行した後には、ロス削減にどれくらいの効果があったか測定する必要があります。その他にも、対策を実施したことで発生した新たな問題点や想定していなかった課題がないかの確認も重要です。現場オペレーターの負担の大きさなど、影響範囲も観測します。
6.改善結果に基づきルールを策定する
改善の効果を検証した結果、効果があった改善策はルールを整理し、全体へ展開できるようルールを策定します。ルールを作成する際には、なぜ効果があったのか具体的な数値をまとめておくことが大切です。
時間や温度、位置など数値を使って許容範囲を記載しておくことで、ロスの再発防止や対策の長期継続への貢献が期待できます。
7.全体へ展開する
標準ルールが定まった後は、全体へロス改善策を展開します。同じ機械であっても条件の違いによって再設定が必要なケースもあるので注意が必要です。ロス削減に必要なスキルがあれば、併せて水平展開します。有用な改善策を全体へ展開することで、会社全体のロス削減につながります。
時代遅れではない最新のTPM活動
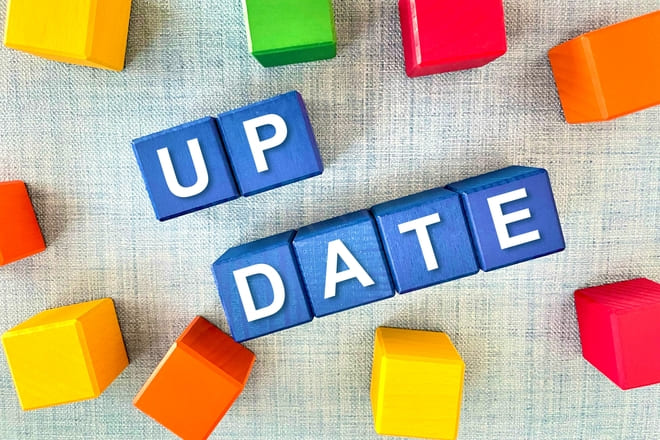
TMP活動は、1971年に提唱されて以来、長期に渡りさまざまな会社で取り入れられてきました。長く取り入れられている一方で、近年ではTPM活動は時代遅れだと考えられることもあります。しかしながらロスをなくし利益を最大化する取り組みは、今の時代だからこそ重要なものです。
ここからは、時代遅れではない最新の技術や考えを取り入れた手法について解説します。
戦略的TPM(S-TPM)を導入する
戦略的TPM(S-TPM)とは、TPMを提唱した公益社団法人日本プラントメンテナンス協会が今の時代に合わせ、コンテンツの拡大と充実を図り体系化したものです。TMP活動は下図のように時代に合わせ、進化を続けてきました。
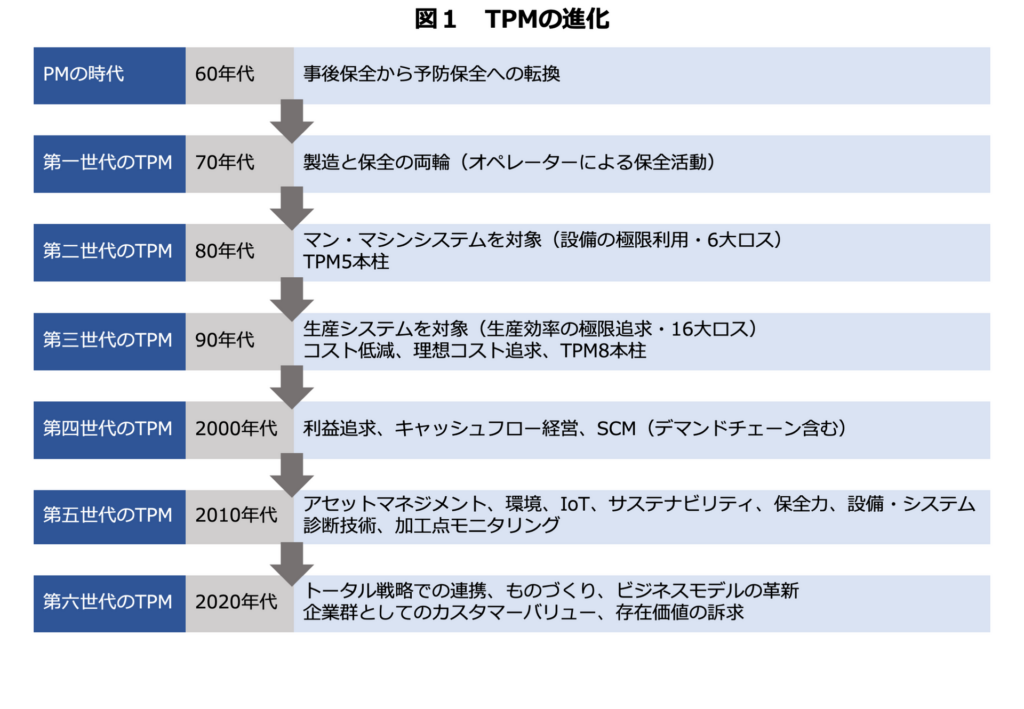
戦略的TPM(S-TPM)では、TPM活動の8本柱のうち管理・間接を充実し、9つの活動をメニューとして追加しています。
活動 | 詳細 |
---|---|
オフィスワーク革新 | ミニマム工数で業務達成 |
ビジネス開発管理 | 将来および新ビジネスの売上増加 |
ビジネスプロセス開発管理 | コスト削減と価値最大化 |
組織価値&戦略革新 | 企業戦略の革新 |
経営&指標管理革新 | 経営指標の改革 |
事業戦略&総資産管理革新 | 長期資産活用の最適化 |
顧客満足&営業革新 | 継続的な顧客満足の向上 |
購買調達革新 | 購買行動の革新 |
プロセス技術革新 | 革新プロセスの生産最適化 |
サプライチェーン革新 | 最適なサプライチェーン構築 |
9つの活動メニューは、すべてを導入する訳ではなく会社によって要不要を判断し取り入れます。戦略的TPM(S-TPM)は、日本だけではなく海外の経営者からも評価されています。
DXの活用
最新のTPM活動をおこなうためには、DXの活用が欠かせません。例えば、Iotとセンサー技術を活用することで、設備を監視し異常をリアルタイムで検知できる仕組みを構築します。他にもAI技術により過去のデータを分析し、最適なメンテナンス時期の測定も可能です。
また、設備の仮想モデルを作成しシミュレーションを行うことで、最適な運用条件を見出すことにも貢献します。このようにDXを活用することで、効率良くロスを削減する効果が期待できます。製造業でのDXについては下記の記事でも解説していますので、ご覧ください。
クラウドを活用したデータ管理
クラウドを活用したデータ管理をおこなうことにより、報告書や設備の稼働状況など、さまざまなデータを会社全体で即座に共有できます。
また、帳票を紙管理している場合、保管スペースが必要で情報を探し出すのに時間がかかりますが、帳票を電子化しクラウドに保管すれば、場所をとらずに情報を簡単に探せるようになりロス削減に役立ちます。帳票の電子化については、下記の記事でも解説していますので、参考にしてください。
モバイルデバイスの活用
スマートホンやタブレットなどモバイルデバイスを活用すると、場所を問わずデータ入力や保管ができるため効率的です。さらにモバイルデバイスにはカメラが付いており、写真や動画の撮影、バーコードやQRコードの読み込みもできます。
従業員のコミュニケーションにも役立ち、リアルタイムで情報を取得できる点もメリットです。
デジタル人材の育成
今後の製造業の現場では、デジタル技術の活用が欠かせません。従来の製造業の技術に加え、データ分析やプログラムなどのデジタルスキルを持った人材を育成していく必要があります。従業員が学習できる環境を用意し、自社に合ったシステムを活用できるよう育てていくのも、最新のTPM活動において重要なポイントです。
「i-Reporter」を活用したTPM活動とは
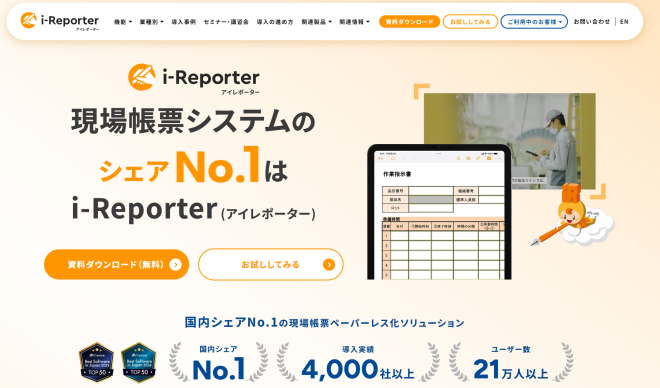
「i-Reporter」は、現場で使用する帳票を電子化する現場帳票システムです。TPM活動におけるロスの削減に「i-Reporter」は役立ちます。ここからは、TPM活動に「i-Reporter」を活用できるポイントを解説します。
ペーパーレス化による業務効率の改善
「i-Reporter」を使い、従来の紙帳票からデジタル帳票へ置き換えると業務効率の改善が見込めます。従来の紙帳票では、保管場所を多く必要としデータが探しにくく、手書きの文字を読み解く必要がありました。
「i-Reporter」では、入力候補やラジオボタンを使った帳票の作成ができ、入力の手間やミスを削減できます。使い慣れた紙帳票やExcelファイルと同じ形式の帳票を簡単に作成できるので、スムーズに移行できます。
クラウドによるリアルタイムのデータ共有
「i-Reporter」のデータは、クラウドに保管されます。クラウドに保存されたデータは、PCだけではなくiPadを使って閲覧や編集が可能です。また、ネットがつながらない場所でもデータの閲覧ができます。
さらにメールを使った通知や承認フローにも活用できるため、ロス削減に貢献します。
写真やQRコードを使用した正確な記録
「i-Reporter」はiPadで利用できるため、写真やQRコードを使用して正確な記録が取れる点がメリットです。機械の状態を伝える際に、文章にして説明するよりも写真や動画で見せた方が瞬時に内容が伝わります。機械からデータを読み込む際にもQRコードを活用すれば、入力ミスなく正確に記録できます。
IoTやAIとの豊富な連携機能
「i-Reporter」は、多岐にわたるハードウェアやソフトウェアと連携が可能です。製造業の設備制御に使われるPLCと連携させ、自動で情報を取得されることもできます。その他にも、データベース上の情報を連携して取得でき、「i-Reporter」にある情報を外部のソフトウェアへ渡すことも可能です。
作業工数の把握
作業開始・終了時にタブレットのボタンを押すよう習慣づければ、個人ごとに作業効率を測定することができます。ロスをなくすTPM活動では、現状の把握が最も大切です。原因を突き止め改善を図る際に「i-Reporter」を活用できます。
「i-Reporter」は導入社数No.1(富士キメラ総研 2024年8月8日発刊)、国内トップシェアを誇る現場帳票システムです。
導入することで、紙の現場帳票の「記入・報告・管理」すべてのペーパーレス化を実現し、さまざまな業務の効率化やDXにつなげられます。
また、弊社株式会社サンソウシステムズでは、要件定義から設計・導入、その後の運用管理まで、お客様に寄り添った伴走支援が可能です。
ぜひ、ご一緒に現場の業務課題を整理していきましょう。サービス資料を用意しましたので、併せてこの機会にこちらから無料でダウンロードしてみてください。
導入実績3,500社以上
TPM活動を導入し生産性を向上しよう
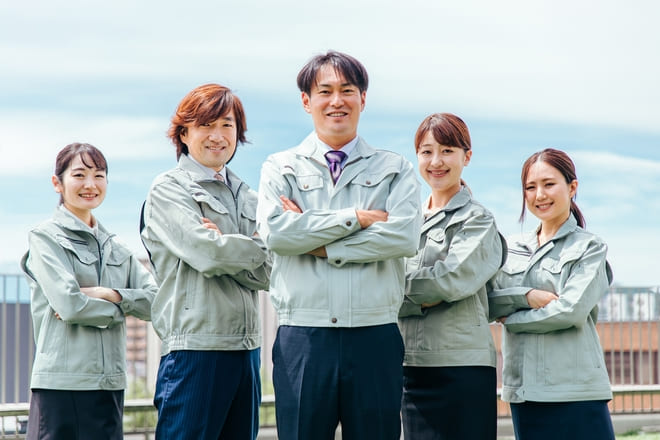
会社の利益を守り成長していくためには、無駄の削減が欠かせません。TPM活動によりロスをなくせば、効率の良い経営状態を保てます。現場の従業員にとってもスムーズで無駄のない仕事を自ら考え実行することは、モチベーションアップにつながります。
今回の記事を参考に、最新のTPM活動を取り入れ、より効率の良い製造業の現場を実現し生産性を向上させていただければ幸いです。
株式会社サンソウシステムズでは、導入社数No.1(富士キメラ総研 2024年8月8日発刊)の現場帳票システム「i-Reporter」の導入を支援する『ちょこっと相談室』という無料のオンライン相談窓口を設けております。
現場帳票のシステム化を検討する際、「時間がなくて調査ができない」「導入しても運用できるか不安」「他社製品と比較してどうなのか」といった課題や不安がつきものです。
そのような企業様も安心してください。コンサルティング実績の多い弊社であれば、課題のヒアリングから業務効率化に向けた、目標設定・試験導入、その後の本導入から運用まで伴走支援いたします。
まず、やるべきことを整理するだけでもメリットです。
お話を伺いたい方は、無料の『ちょこっと相談室』(Zoom:オンライン)で、お気軽にご相談ください。現状課題のヒアリングから丁寧に対応させていただきます。