多くの製造業での課題は、生産性の向上や人材不足です。これらの課題を解決する方法として、「生産管理のDX」が注目されています。独立行政法人情報処理推進機構の「DX動向2024」によると、DXに取り組んだ6割以上の企業が成果を出しているため、生産管理においてもDXを推進することで多くの課題解決が期待できます。
本記事では、生産管理DXとは何か、なぜ必要なのかを解説し、解決できる課題や具体的な推進手順、成功事例までを網羅的にご紹介します。さらに、DXを推進するおすすめの現場帳票システム「i-Reporter」や、導入に関するよくある質問にもお答えします。
また、弊社株式会社サンソウシステムズでは、要件定義から設計・導入、その後の運用管理まで、お客様に寄り添った伴走支援が可能です。
ぜひ、ご一緒に現場の業務課題を整理していきましょう。サービス資料を用意しましたので、併せてこの機会にこちらから無料でダウンロードしてみてください。
導入実績3,500社以上
目次
生産管理におけるDXとは
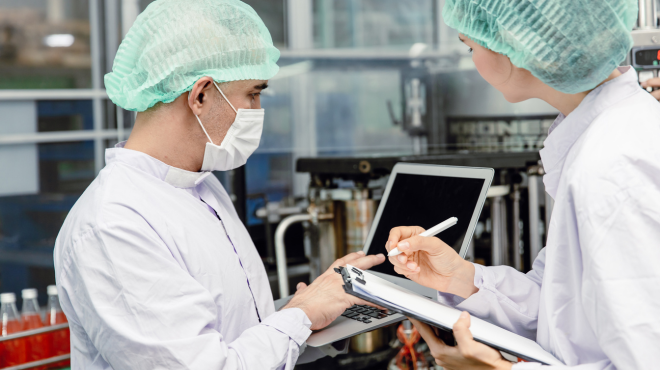
生産管理におけるDX(デジタルトランスフォーメーション)とは、デジタル技術を活用して、複雑化した業務プロセスを効率化・最適化・高度化を図って生産性を向上させる取り組みです。また、DXによって生産管理を変革し、新しい価値の創出、競合他社との優位性を確立することも目的としています。
従来の生産管理システムに加えて、IoTやAI、ビッグデータ解析などの最新技術を導入し、データに基づいた意思決定や自動化・自律化された生産プロセスを実現します。
具体的には、以下のような要素が含まれます。
- 生産プロセスの可視化: IoTセンサーなどを活用して、生産設備の稼働状況、作業者の行動、在庫状況などのデータをリアルタイムに収集し、可視化する
- データ分析による改善: 収集したデータを分析し、ボトルネックとなっている工程や改善の余地があるカ所を特定する
- AIによる最適化: AIを活用して、生産計画の最適化、品質管理の自動化、異常検知などをおこなう
- 自動化・省人化: ロボットや自動化設備を導入して人手による作業を減らし、生産効率を高める
- サプライチェーンとの連携: サプライヤーや顧客との情報連携を強化し、需要予測の精度向上や納期短縮を実現する
これらの取り組みを通じて、企業は生産性の向上、コスト削減、品質向上、納期遵守率の向上などを実現し、競争力を強化できます。
経済産業省によると、DXに取り組む企業は年々増加しており、着実にDXが企業に浸透していることが明らかになりました。
また、DXで成果を残している中堅・中小企業などDXのモデルケースとなる優良事例を「DXセレクション2025」として選定するなど、企業規模・業種に関わらずDXが推進されていることがわかります。
生産管理においても、DXは欠かせない存在となっています。
参考:独立行政法人情報処理推進機構の「DX動向2024」
経済産業省「DXセレクション2025を選定しました」
生産管理のDXが必要な理由
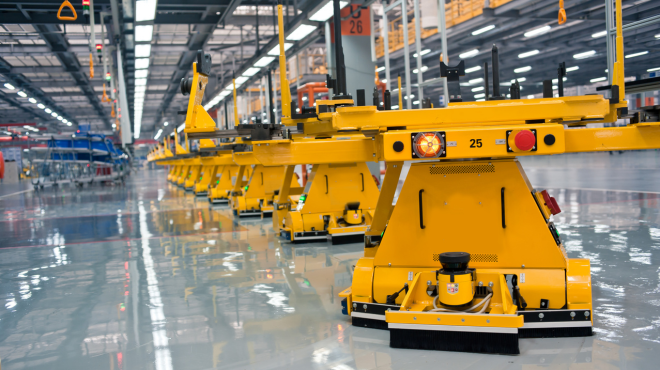
生産管理におけるDXは、製造業が持続的な成長を遂げるための必要不可欠な戦略です。本章では、生産管理のDXが求められる理由を5つの視点から解説します。
生産プロセスの自動化・最適化
DXを推進することで、これまで人の手で行っていた作業を自動化し、生産プロセス全体の最適化が可能です。
生産管理のプロセスは複雑なため、人的リソースが大きいだけでなく製品を一定の品質に保てないことがあります。品質の低下は工程が複雑化することから業務内容を各工程で共有できず、生産品質が低下している段階で対処できないからです。
DXによって、業務効率化が進むことはもちろん、手作業によるミスを減らし、効率的な生産体制を構築できます。例えば、IoTセンサーを活用して設備の稼働状況をリアルタイムに監視し、異常を検知すれば自動でメンテナンスをおこなうといったことが可能になります。
人材不足の解消と業務効率化
少子高齢化が進む日本では、製造業における人材不足が深刻化しています。生産管理のDXは、業務を自動化し、AIを活用して計画業務を支援することで、少ない人数でも効率的な生産活動が可能です。人的リソースをより高度な業務に集中できるため、人材不足の解消が期待できます。
また、動画マニュアルの作成やナレッジデータベースの構築といったDXを促進することで、ベテランの技術や知識をデジタル化し、若手への技術継承を効率化することも可能です。人材の育成や異動にも活かせるでしょう。
コスト削減と収益向上
DXによる生産プロセスの最適化は、コスト削減に直結します。例えば、IoTやAIを活用して需要予測の精度を高め、在庫の最適化を図ることで過剰在庫や欠品による損失を減らせます。
また、設備の故障を予測し、計画的にメンテナンスすることで、突発的な設備停止による生産ロスも防ぐことが可能です。これらの取り組みにより、収益向上に貢献します。
変化への対応力強化と競争力向上
市場のニーズは常に変化しており、企業は変化に柔軟に対応する必要があります。特に技術の急速な発展によりAIなどで技術を模倣できることになれば、生産性の向上で競争力を維持しなければ衰退してしまう可能性があるでしょう。
生産管理のDXを推進することで、市場の動向や顧客のニーズをリアルタイムに把握し、迅速に生産計画を修正できます。
また、サプライチェーン全体を可視化し、リスクを早期に発見することでサプライチェーンの生産停止を防ぐことも可能です。変化への対応力を高めれば、競争優位性も確立できます。
新たなビジネスモデルの創出
市場のニーズは多様化しており、常に新しい変化を求められている時代です。既存のビジネスモデルにおける需要が減少すれば、いずれは競争力を維持するのは困難になります。
DXは、コストやリソースを確保して既存のビジネスモデルに変革をもたらせるものであるため、新たなビジネスモデルを創出できる可能性があります。
例えば、顧客のニーズに合わせて製品をカスタマイズし、オンラインで直接販売することが可能です。また、製品の利用状況を収集したデータを活用して新たなサービスの開発もできます。DXは、企業に新たな収益源をもたらし、ビジネスの可能性を広げる存在と言えるでしょう。
生産管理のDXで解決できる課題
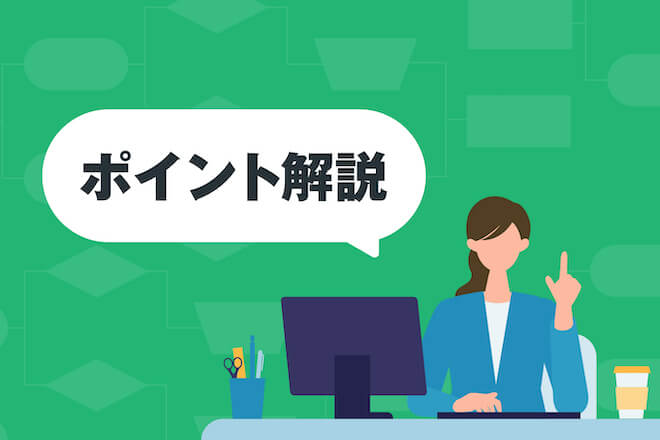
生産管理DXを推進することで、製造業が抱えるさまざまな課題を解決し、競争力強化につなげられます。本章では、具体的な課題とDXによる解決策を解説します。
煩雑な手作業と情報共有の遅れ
従来のアナログな生産管理では、現場での記録や報告が手作業でおこなわれることが多く、転記ミスや集計作業に時間がかかっていました。また、情報共有も紙やメールが中心で、スムーズに業務が進まないこともあります。
生産管理のDXを進めることで、業務の自動化やリアルタイムな情報共有が可能になります。
例えば、現場帳票の電子化により、紙への記録作業による時間ロスやヒューマンエラーの改善が可能です。入力されたデータはリアルタイムで集計・分析され、関係者間で共有されるため、迅速な意思決定ができます。また、ペーパーレス化によるコスト削減や環境負荷低減にも貢献します。
在庫管理の精度低下と過剰在庫・欠品
手作業による在庫管理では、正確な在庫数の把握が難しく、過剰在庫や欠品が発生しやすい状況でした。過剰在庫は保管コストの増加や廃棄ロスの発生につながり、欠品は生産計画の遅延や顧客満足度の低下を招きます。
DXによって、在庫状況をリアルタイムに可視化し、適切な在庫量を維持することが可能です。
例えば、在庫管理システムの活用で仕掛品管理を効率化できます。各工程の仕掛品の所在や数量、状態をリアルタイムに把握することで、滞留在庫の削減や、必要な時に必要な量の部品を供給することが可能になります。また、需要予測に基づいた自動発注システムを導入することで、欠品リスクを低減し、最適な在庫量の維持もできます。
生産計画の精度低下と納期遅延
経験や勘に頼った生産計画では、需要変動や設備の故障など予期せぬ事態に対応できず、納期遅延が発生する可能性があります。また、計画変更に柔軟に対応できないため、生産効率の低下を招くこともあるでしょう。
DXを導入することで、リアルタイムなデータに基づいた精度の高い生産計画を立案し、納期遵守率※を向上させることが可能です。
例えば、過去の生産実績や市場動向などのデータを分析し、AIを活用した需要予測でより正確な生産計画を立案できます。また、生産ラインの稼働状況や設備の故障状況をリアルタイムに監視し、計画変更に柔軟に対応することで、納期遅延を最小限に抑えられます。
※納期遵守率:納期通りに製品を出荷できた割合を示す指標
品質管理の徹底と不良品の削減
目視検査に頼った品質管理では、検査員の知識や経験によって品質にばらつきが生じ、見落としによる不良品の流出を防ぐことが難しい状況でした。また、不良原因の特定に時間がかかり、再発防止策を講じるまでに時間がかかることもあります。
DXによって、品質管理を自動化・高度化し、不良品の発生を抑制することが可能になります。
例えば、画像認識AIを活用した外観検査システムを導入することで、目視検査では見落としがちな微細な欠陥の自動検出が可能です。また、品質データをリアルタイムに分析し、不良発生の傾向を早期に発見することで、未然に不良品の発生も防げます。品質記録のExcelへの転記を電子化すれば、人員や時間の削減にもつなげられます。
コスト増と収益悪化
生産管理における課題が複合的に影響し、製造コストの増加や収益の悪化を招く可能性があります。無駄な在庫や納期遅延による顧客からの信頼低下、不良品の発生などは、企業の収益を圧迫する要因です。
生産プロセスの最適化や在庫管理の効率化、品質管理の徹底などによってDXを推進することで、無駄なコストを削減し、収益性を向上できます。また、顧客ニーズに合わせた製品を迅速に提供することで顧客満足度を高め、リピート率向上につなげることも可能です。
生産管理DXを推進する5つの手順
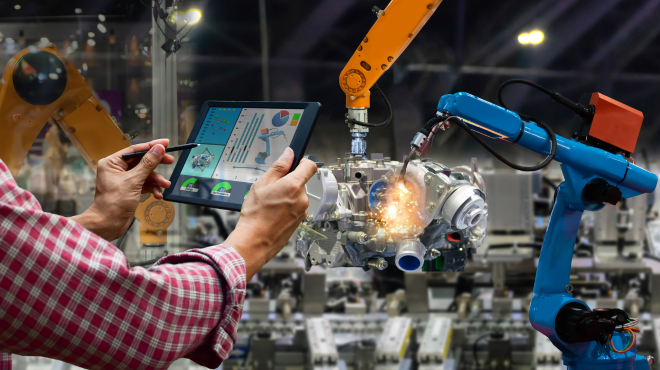
生産管理DXを成功させるためには、段階的なアプローチが不可欠です。本章では、生産管理DXを推進する5つの手順を解説します。
1.現場の把握と洗い出し
まず、現状の生産現場を詳細に把握します。現場の担当者へのヒアリングや、実際の作業フローの確認を通じて、課題や改善点、そしてDXによって解決したい問題を明確に洗い出します。
現場の意見を尊重して課題を共有し、DX推進への協力体制を築くことが重要です。
具体的には、以下の項目について調査・分析をおこないます。
- 業務プロセス:各工程における作業内容、使用ツール、情報フローなど
- 課題:非効率な作業、ボトルネックとなっている工程、人的ミスが発生しやすいカ所など
- データ:収集・管理しているデータの内容、形式、活用状況など
- システム:既存のシステム構成、機能、連携状況など
2.目標設定とKPIの設定
現場の課題を洗い出した後は、DXによって達成したい具体的な目標を設定します。目標は、売上向上やコスト削減、生産性向上など、経営戦略と整合性のとれたものである必要があります。
目標を設定したら、達成度を測るためのKPI(重要業績評価指標)を設定します。KPIは数値で測定可能な指標を選定し、定期的にモニタリングすることで、DXの進捗状況の把握が可能です。
以下はKPIの例です。
目標 | KPI |
生産性向上 | 単位時間あたりの生産量、不良品率の低下、サイクルタイムの短縮 |
コスト削減 | 原材料費の削減、エネルギーコストの削減、在庫コストの削減 |
納期遵守率向上 | 納期遅延件数の削減、リードタイムの短縮 |
3.最適なツールの選定
目標とKPIが明確になったら、達成するために最適なツールを選定します。
生産管理システムや現場帳票電子化ツール、IoTセンサー、AI分析ツールなど、さまざまなツールの中から、自社の課題や目標に合わせて必要な機能を備えたツールを選びます。
また、ツールの機能だけでなく、導入費用や運用コスト、保守費用も考慮に入れる必要があります。既存システムとの連携性も選定基準として考えましょう。
4.導入計画の策定とDXの実施
ツールを選定したら、導入スケジュール、担当者、予算などを明確にし、具体的な導入計画を策定します。
導入時には、現場の担当者へのトレーニングを十分に行い、新しいツールを使いこなせるようにサポートすることが重要です。また、導入初期段階では、想定外の問題が発生する可能性もあるため、綿密なテストと検証をおこなうようにしましょう。段階的に導入範囲を拡大していくことでリスクを最小限に抑えられます。
5.効果測定と改善
DXの実施後は、KPIを定期的にモニタリングして効果測定をおこないます。
効果測定の結果は今後のDX推進の参考となるため、詳細な分析をおこない記録しておくことが重要です。また、現場担当者からのフィードバックも積極的に収集し、改善に役立てましょう。PDCAサイクル(計画、実行、評価、改善)を回し続けることで、DXの効果を最大化できます。
生産管理DXの成功事例
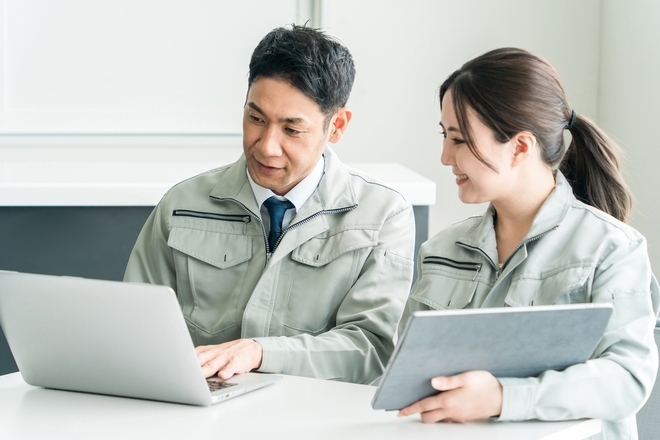
本章では、生産管理DXを導入し、実際に成果を上げている企業の事例を3つご紹介します。これらの事例から、自社のDX推進のヒントを見つけていきましょう。
現場帳票の電子化で、紙への記録作業による時間ロスやヒューマンエラーが改善
NTPT Company Limitedは、タイで東南アジア圏内における生産拠点として、ブベアリングの旋削加工や等速ジョイント外輪の鍛造・旋削などをメインに展開する部品加工メーカーです。
同社では、紙帳票への製造数や問題事象などの記録ミスによるヒューマンエラー、紙帳票からExcelへの再入力による作業過多が課題となっていました。
そこで「i-Reporter」を導入します。紙への記録作業による時間ロスやヒューマンエラーが改善され記録作業の効率化、正確なデータで分析をおこなうことにより生産工程の効率化が実現しました。
「i-Reporter」は導入社数No.1(富士キメラ総研 2024年8月8日発刊)、国内トップシェアを誇る現場帳票システムです。
導入することで、紙の現場帳票の「記入・報告・管理」すべてのペーパーレス化を実現し、さまざまな業務の効率化やDXにつなげられます。
また、弊社株式会社サンソウシステムズでは、要件定義から設計・導入、その後の運用管理まで、お客様に寄り添った伴走支援が可能です。
ぜひ、ご一緒に現場の業務課題を整理していきましょう。サービス資料を用意しましたので、併せてこの機会にこちらから無料でダウンロードしてみてください。
参考:株式会社シムトップス「NTPT Company Limited様 導入事例」
品質記録のExcelへの転記を電子化し、人員や時間を削減
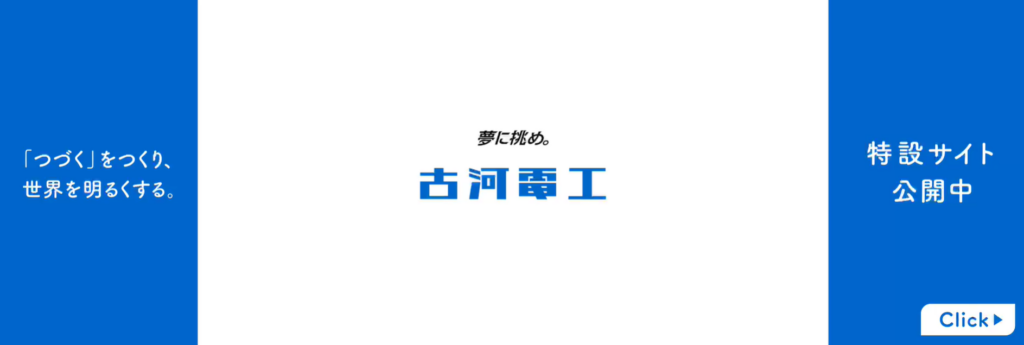
古河電気工業株式会社は光ファイバ・電線・ワイヤーハーネスなどの製造を行なう非鉄金属メーカーです。
DXに取り組む前の課題として、品質記録として作業日誌や設備点検記録表をすべて紙に書いて保管していたため、ファイリングだけで毎月200分もの時間がかかっていました。
また、帳票保管には年間でおよそ15,000枚の紙を使用し品質問題が出た際は製造工程に問題が発生していないかを確認するため、原因解明に至るまでのプロセスに数日間かかっていたそうです。
現場帳票のペーパーレス化ツール「i-Reporter」を導入した結果、膨大な紙からの検索時間が20分から5分以内に削減しました。また、紙からExcelへの転記などにかかっていた人員や時間などの管理コスト削減にも成功しています。
さらに、ファイリングを200分から0分に削減でき、年間15,000枚の帳票を保管していた管理スペースも不要になるなど、さまざまな効果を得ています。
参考:株式会社シムトップス「NTPT Company Limited様 導入事例」
所在管理システムの活用で仕掛品管理を効率化
金属製品製造業を営む企業では、多くのお客様から製品を預かって加工するため、お客様によって異なる受け入れ日・作業日・出荷日の管理に手間がかかっていました。また、製品を倉庫から探し出すのに1日約7時間~20時間かかることもあり、業務効率化の低下や残業時間の増加に課題を感じていました。さらに、探索業務に時間がかかるあまり、製造ラインへの投入が遅れることもあったそうです。
課題を解決するため、所在管理システムを導入しました。作業指示書の伝票番号を管理システムに入力することで、仕掛品の在庫場所が一目でわかるようになり、製品を探し出す時間の90%削減につなげています。また、探索時間が大幅に減ったことで、製造ラインへの投入が遅れることも少なくなり、稼働率も高まっています。
参考:シュナイダーエレクトリックホールディングス株式会社・アドソル日進株式会社「所在管理システムを使って探索業務のムダを削減!仕掛品の在庫置き場管理 導入事例」
生産管理DXを成功させるポイント
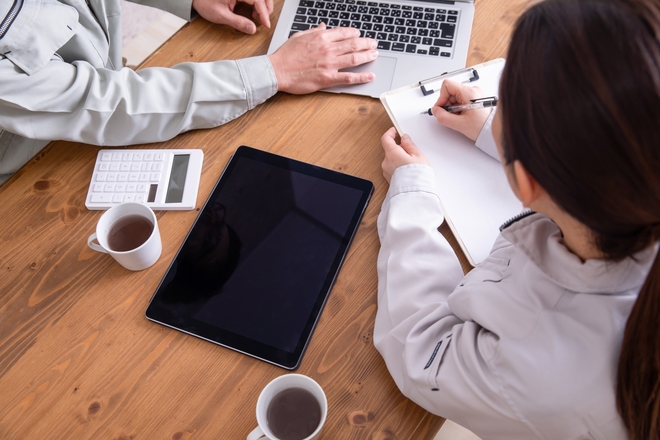
生産管理DXを推進する上で、いくつかの重要なポイントがあります。本章では3つのポイントを解説します。
スモールスタートで実施する
DXは全社的な大規模プロジェクトとして捉えがちですが、最初からすべての業務をデジタル化しようとすると、失敗するリスクが高まります。特にDXに初めて取り組む場合は対応に慣れていないことから、現場の混乱を招きやすくなり最悪の場合、稼働が停止してしまう可能性もあります。
まずは、特定の部門やプロセスに焦点を当て、小さく始めることが重要です。スモールスタートで成功を積み重ねることで、他の部門への展開もスムーズに進められます。
例えば、まずは現場帳票の電子化から始める、特定の製品ラインの在庫管理システムを導入するなど、範囲を限定して効果を検証しましょう。
現場の理解・同意を得る
DXは、現場の業務プロセスを大きく変える可能性があります。そのため、現場の従業員の理解と協力が不可欠です。DXの目的やメリットを丁寧に説明し、現場の意見を積極的に取り入れることで、抵抗感を減らし、スムーズな導入を促せます。
現場の従業員を巻き込み、共にDXを推進する体制を構築することが重要です。また、社員の負担にならないような配慮も欠かせません。
例えば、DX導入前に説明会を開催し、導入後も定期的にフィードバックを求める場を設けることが有効です。
システムを導入する
生産管理におけるDXを成功させるためには、適切なシステムの導入が不可欠です。自社の課題やニーズを明確にし、それに合ったシステムを選定します。システム導入後も、定期的なメンテナンスやアップデートをおこない、常に最新の状態を保つことが重要です。
また、従業員への教育・研修も徹底し、システムを最大限に活用できる体制を整えましょう。
以下はシステムを導入するにあたっての注意点です。
- 自社の課題を明確にする
- 必要な機能を洗い出す
- 費用対効果を検討する
- ベンダーのサポート体制を確認する
- トライアル期間を活用する
ポイントを踏まえて最適なシステムを導入することで、生産管理DXの成功が期待できます。
生産管理DXシステムおすすめ3選
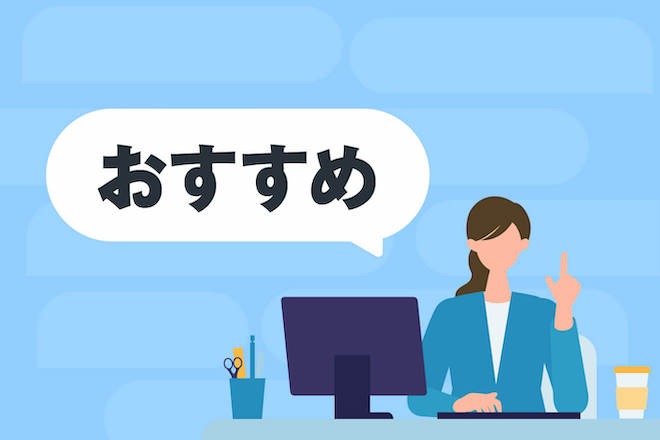
生産管理DXを成功させるためには、自社の課題や目的に合ったシステムの導入が不可欠です。ここでは、特におすすめの生産管理DXシステムを3つご紹介します。
i-Reporter
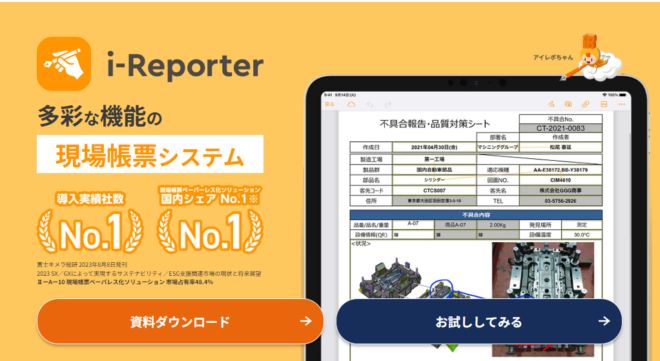
i-Reporterは、国内トップシェアを誇る現場帳票システムです。
紙帳票の入力作業をパソコンやタブレット、スマートフォンでおこなえるようにすることで、入力ミスや転記の手間を削減し、業務効率化に貢献します。使い慣れた帳票をそのまま移行できるため、現場の担当者も安心して利用できます。
また、録音機能や写真添付機能など、現場での使いやすさを追求した機能が豊富に搭載されていることが特徴の一つです。
項目 | 詳細 |
機能 | 現場帳票の電子化、録音、写真添付、週報・月報自動作成 |
特徴 | 現場での使いやすさを追求、多様な帳票に対応 |
おすすめポイント | 紙帳票からの脱却、データ入力業務や在庫管理、施工管理業務の効率化 |
UMWELT
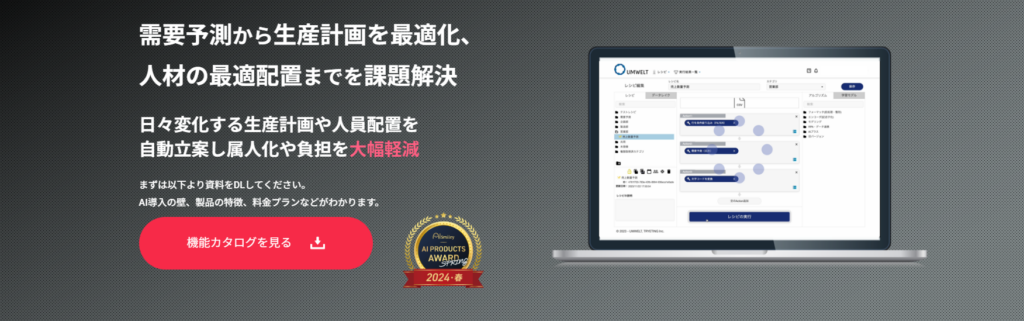
UMWELTは、需要予測や生産計画、在庫管理、品質管理など幅広い業務のAI予測ツールです。
データに基づいた最適な生産管理や在庫管理を実現するため、生産管理全体のDXを進めたい方におすすめです。また、既存の生産管理システムへのAPI連携も容易で、スムーズに導入できます。
さらに、ツールの使い方のレクチャーや運用サポートなど、充実したサポート体制があるため、はじめてツールを導入する方でも安心です。
項目 | 詳細 |
機能 | 需要予測、生産計画、在庫管理、品質管理 |
特徴 | オールインワン、API連携による柔軟な拡張性 |
おすすめポイント | 生産管理全体の最適化、データを基にした意思決定 |
スマートマットクラウド
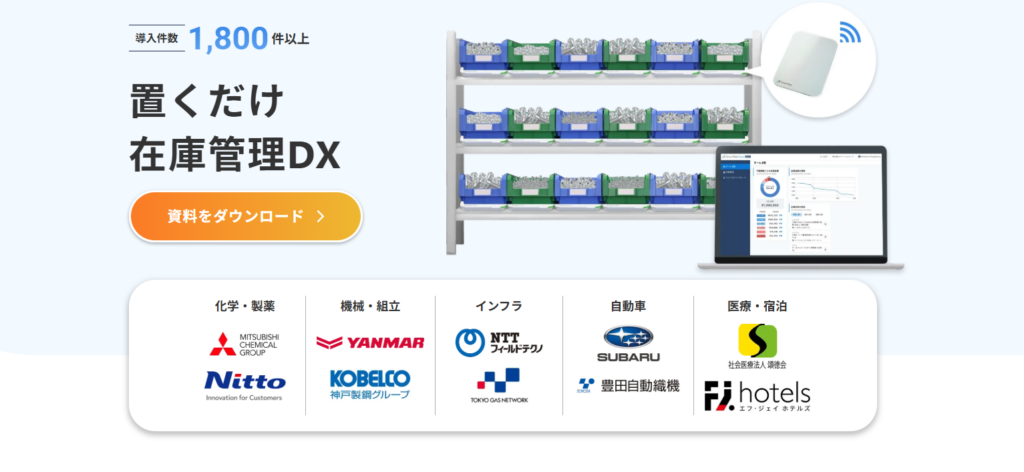
スマートマットクラウドは、在庫管理の自動化に特化したシステムです。在庫を載せたマットの重量を自動で計測し、クラウド上でリアルタイムに在庫状況を把握できます。
過剰在庫や欠品を防止し、在庫管理コストの削減に貢献するため、特に多品種少量生産をおこなっている企業や、在庫スペースが限られている企業におすすめです。
項目 | 詳細 |
機能 | 在庫自動計測、リアルタイム在庫管理、アラート機能 |
特徴 | 設置が容易、省スペース |
おすすめポイント | 在庫管理の自動化、適正在庫の維持 |
生産管理DXに関するよくある質問
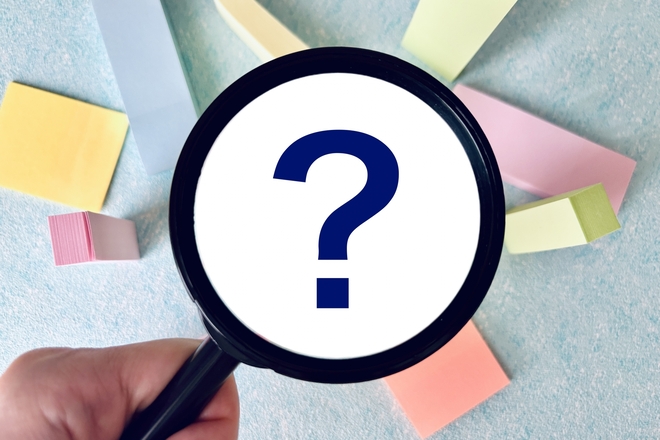
本章では、生産管理DXに関するよくある質問を解説します。
Q1:DXって何から始めれば良いの?
DX推進の第一歩は、現状の課題を明確に把握し、目指すべきビジョンを描くことです。
まずは、自社の生産管理プロセスにおける課題を洗い出し、どのような状態を目指したいのか、具体的な目標を設定します。
その上で、目標達成のために必要なツールや技術を選定し、スモールスタートで導入・検証を繰り返しながら、徐々に範囲を拡大していくのがおすすめです。ビジョンの明確化はDXを成功させるために不可欠です。
Q2:中小企業でも導入できる?
中小企業でも十分に生産管理DXを導入できます。特定の業務プロセスに特化したツールを導入し、効果を検証しながら徐々に範囲を拡大していくのがおすすめです。システムを導入する際は、複数のシステムを比較して、費用対効果をチェックしましょう。
Q3:生産管理DXの費用目安は?
生産管理DXの費用は、導入するシステムの種類や規模、カスタマイズの範囲によって大きく異なります。月額数万円から利用できるものもありますが、大規模なシステムを導入する場合には数百万円以上の費用がかかることもあります。導入前に複数のベンダーから見積もりを取り、費用対効果を比較検討することが重要です。
Q4:従業員のITスキルが低くても大丈夫?
従業員のITスキルに不安がある場合でも、生産管理DXは可能です。導入するシステムを選ぶ際には、操作が簡単で、従業員が使いやすいものを選ぶことが大切です。
また、ベンダーによっては、導入支援や研修サービスを提供している場合もあるため、積極的に活用することをおすすめします。現場の理解と同意を得ながら進めることが重要です。
AI活用による生産管理DXの将来性
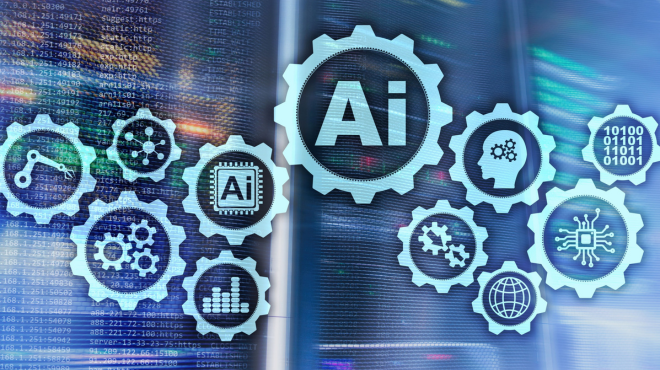
AI(人工知能)の進化は、生産管理DXの将来に大きな可能性をもたらしています。AIを活用することで、これまで人間が行ってきた複雑な判断や作業を自動化し、生産効率や品質の向上が期待できます。
例えば、AIを活用した生産計画では、過去のデータや市場の動向を分析し、需要予測や在庫管理の精度を向上させることが可能です。これにより、過剰生産や欠品のリスクを低減し、最適な生産量を維持できます。
実際に、AIや生成AIを使用しない企業と比較して、AIで得たデータを活用する企業ほどDXの成果が出ていることが明らかになりました。AIや生成AIがさらに普及すれば、多くの企業で新製品・サービスの創出や、既存製品・サービスの高度化が期待できるでしょう。
また、AIは品質管理にも革新をもたらします。AIを搭載した画像認識システムは、製品の欠陥や不良を自動的に検出し、人手による検査作業の大幅な削減が可能です。これにより、品質管理の徹底と不良品の削減を実現し、顧客満足度の向上に貢献します。
さらに、AIは設備の故障予測やメンテナンスにも活用できます。AIが設備の稼働データを分析し、故障の兆候を早期に発見することで、計画的なメンテナンスを実施し、設備の停止時間を最小限に抑えられるでしょう。
システム構築の初期段階でフローを確立する必要がある点や、導入コストが高い点などのデメリットはあるものの、AIの進化は、生産管理DXをさらに加速させ、製造業の競争力を高める上で不可欠な要素となります。中小企業においても、AIツールを積極的に活用し、生産管理の効率化と高度化を図ることが重要です。
i-Reporterの導入で生産管理のDX化実現へ
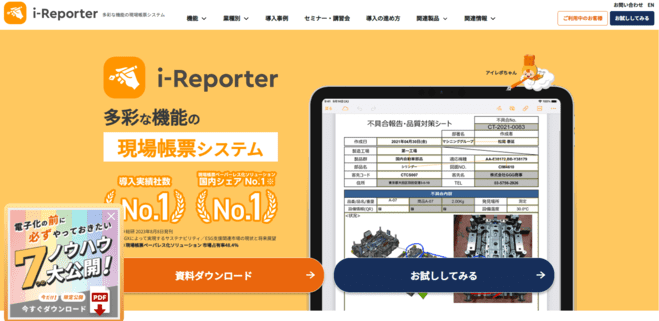
本記事では生産管理DXについて詳しく解説しました。競合他社との競争優位性を確立するためにはDXの取り組みは非常に重要です。
ニーズが多様化する時代において業務を効率化し、常に新しい価値を創出することが求められます。ぜひ、本記事を参考に生産管理のDXを検討してみてはいかがでしょうか。
また、DXにおいて「どのようなツールを選んで良いかわからない」という方は「i-Reporter」の導入がおすすめです。
株式会社サンソウシステムズでは、導入社数No.1(富士キメラ総研 2024年8月8日発刊)の現場帳票システム「i-Reporter」の導入を支援する『ちょこっと相談室』という無料のオンライン相談窓口を設けています。
現場帳票のシステム化を検討する際、「時間がなくて調査ができない」「導入しても運用できるか不安」「他社製品と比較してどうなのか?」といった課題や不安がつきものです。
コンサルティング実績の多い弊社であれば、課題のヒアリングから業務効率化に向けた、目標設定・試験導入、その後の本導入から運用まで伴走支援いたします。
まず、やるべきことを整理するだけでもメリットになります。ぜひ一度、無料の『ちょこっと相談室』(Teams:オンライン)でお気軽にご相談ください。