製造業で働いていれば、常に在庫のことを考えている方も多いのではないでしょうか。
過不足なく、製品の市場に合わせた適切な在庫を考え続けるのは、簡単ではありません。
今回は、製造業界での在庫削減の重要性と、失敗しない在庫削減の方法を徹底解説します。効果的な在庫管理の手法を学び、経営効率を向上させましょう。
「i-Reporter」は導入社数No.1(富士キメラ総研 2023年8月8日発刊)、国内トップシェアを誇る現場帳票システムです。
導入することで、紙の現場帳票の「記入・報告・管理」すべてのペーパーレス化を実現。さまざまな業務の効率化やDX促進につなげられます。
ぜひ、ご一緒に現場の業務課題を整理していきましょう。サービス資料を用意しましたので、併せてこの機会にこちらから無料でダウンロードしてみてください。
導入実績3,500社以上
在庫削減をおこなう目的
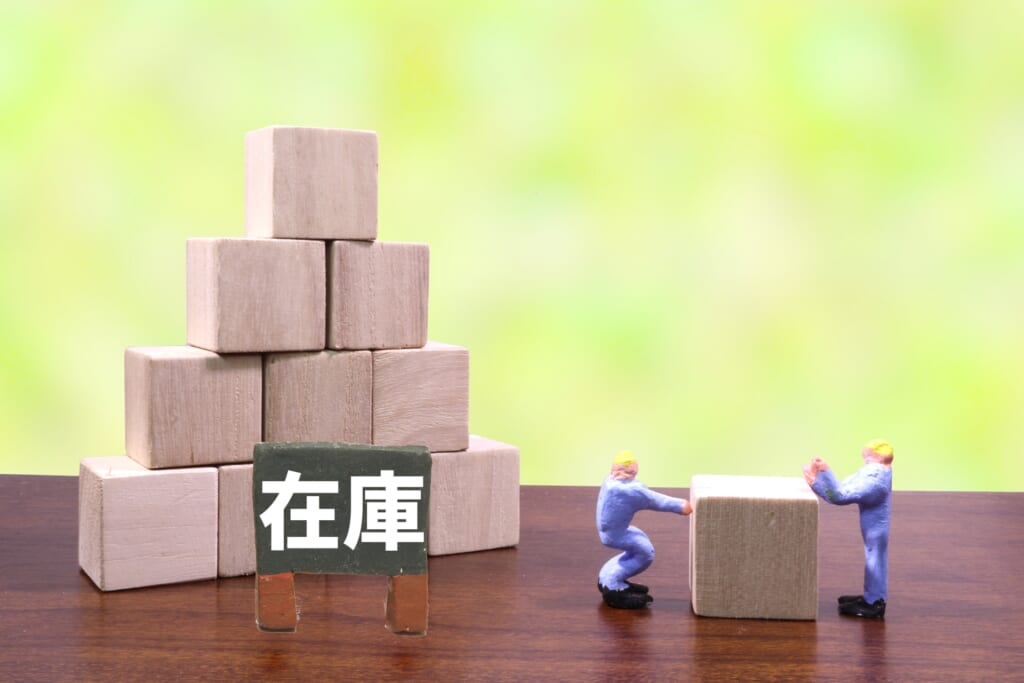
そもそも在庫削減とは在庫管理の工程の1つで、企業経営の上で重要な要素です。管理の対象になるものは、原材料や資材、部品、仕掛品などが挙げられます。在庫削減の成功には多くのメリットがあります。ここではメリットを紹介します。
在庫管理のコストを削減
在庫を多く抱えていると、管理にかかる費用も増大します。例えば、保管スペースの確保・維持費や棚卸しにかかる人件費もランニングコストです。
加えて、売れ残った在庫の場合は、廃棄コストも嵩みます。在庫削減をすると、それらの無駄なコストや作業工数、人件費の最適化が可能です。在庫削減を上手くおこなえば、企業の収益性を向上させられます。
キャッシュフローの改善
在庫削減で得られる大きなメリットは、キャッシュフローの最適化です。在庫になる商品は、現金が商品になった資産であるという認識が重要です。
つまり、資金が在庫という形で固定されていることを指します。
売れ残った在庫は、仕入れに使用した費用を回収し利益を生み出せない上、現金のように他の用途に使用できません。そのため、抱えているだけでコストを生み出す無駄な資産になってしまいます。
そこで、適切な在庫削減は資金の流動性を高めて、より柔軟に資金の運用を可能にします。適切な資金の運用ができれば、キャッシュフローの悪化を防げます。
在庫だけでなく、製造ラインの問題を改善できる
在庫削減の工程の中で、製造ラインの問題点を発見できます。例えば、在庫情報が正確に伝達・共有がされておらず無駄な在庫が発生してしまう、人員配置が足りていない、もしくは過剰に配置されているなどの不適切な人員配置をしているといった在庫以外の問題も洗い出せます。
在庫削減を通して、無駄な人件費のカットや製造フローの最適化をおこなえるのもメリットです。
品質の安定化
在庫の種類によっては長期間保管ができるものもありますが、保管期間が長くなればなるほど商品の品質は低下します。
商品の品質の低下は、顧客満足度の低下や販売できずに廃棄になり余分なコストにつながります。在庫削減は、品質の維持も可能です。
過剰在庫のリスク
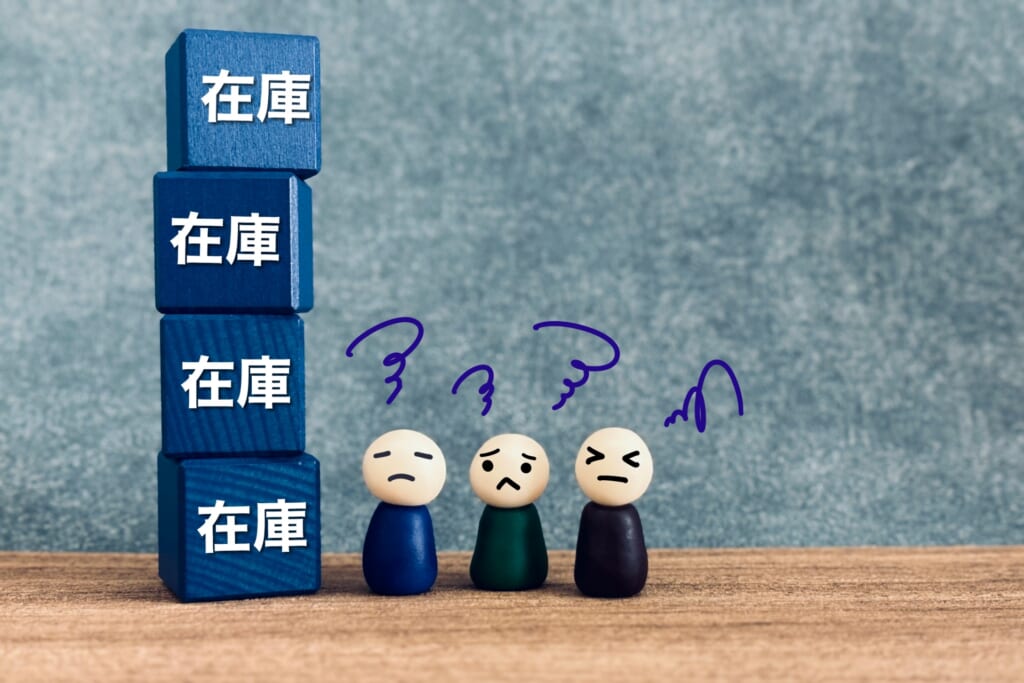
過剰在庫とは、企業が在庫をたくさん抱えることです。過剰在庫は、欠品を防ぎ想定外の需要にも臨機応変に対応ができるため、機会損失を防げます。
しかし、過剰在庫にはいくつかの重大なリスクが伴います。これらのリスクを理解し、適切な在庫管理は企業の健全な経営には不可欠です。
次に、過剰在庫のリスクを紹介します。
在庫の価値という資産価値が下がる
過剰在庫を抱えると、在庫の価値が時間とともに減少します。特に市場の変化が早い電子機器やファッションアイテムなどは短時間で価値が下がりやすいです。
過剰在庫にした分が売れ残ると、値引き販売や最悪の場合破棄につながり、余分なコストの発生につながるリスクがあります。
余分なコストの発生は、企業のキャッシュフローを悪化させ健全な経営を難しくするため、厳重な注意が必要です。
保管場所や管理者といったコストがかかる
過剰在庫は、保管場所や管理者といったコストを増大させます。例えば、保管スペースを追加で確保するとなった場合の、倉庫の賃貸料や保管設備費の増加です。
その他、保管スペースや在庫管理をおこなう管理者の管理範囲が増えるため、管理者一人にかかる負担が増えたり、追加の人員が必要になったりと人件費も多くかかります。
また、人件費だけでなく、在庫の監視や管理に専用のシステムやソフトウェアが必要な場合は、それらの導入や運用にも費用が発生します。
過剰在庫を減らすには、適切な在庫管理システムを導入し、在庫の適正化が重要です。これにより、在庫の価値を最大限引き出し、コストを削減できます。適正在庫は企業が健全な経営を維持する上で、重要な要素です。
在庫削減の方法
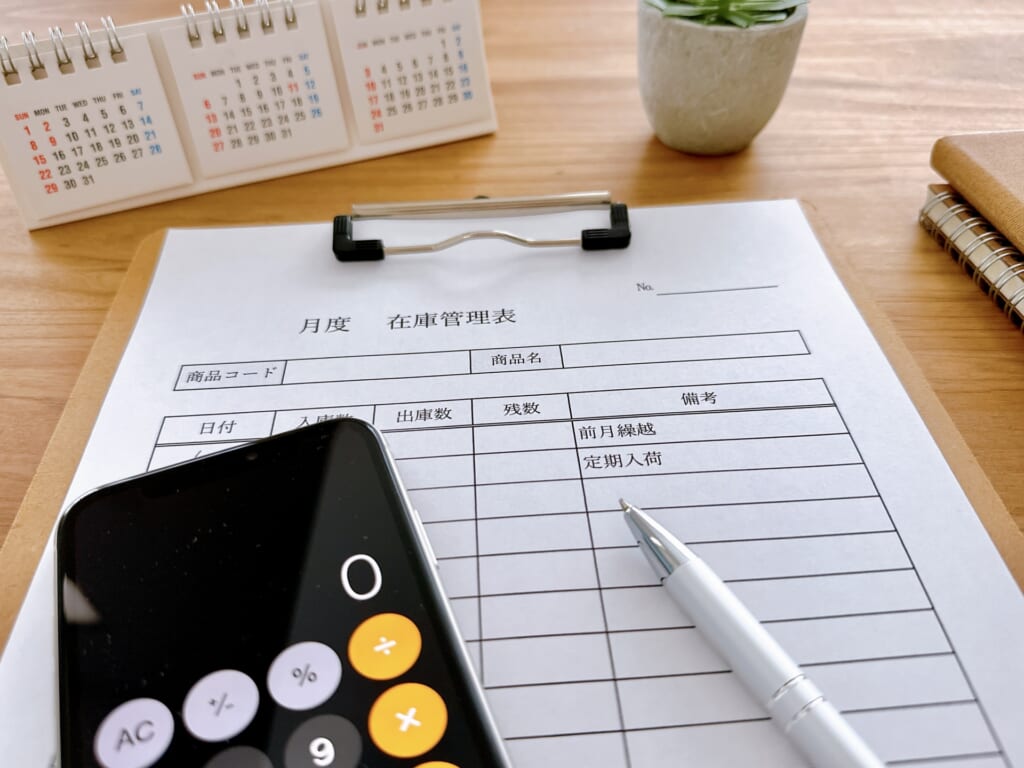
在庫削減は、経営効率向上の重要な課題です。
次に、在庫削減を成功させる方法を紹介します。企業に適した方法をぜひ実践してください。
3Sと5Sを徹底する
在庫削減の工程では、3S(整理・整頓・清掃)と5S(整理・整頓・清掃・清潔・しつけ)が重要だと言われています。これらは在庫削減だけでなく、工場などの職場環境の改善を目的とした手法です。
3Sと5Sの徹底で在庫の無駄を減らし、効率的な在庫管理が可能です。例えば、整理によって不要な在庫を排除し、整頓によって必要な在庫をすぐに確認できる環境を作ります。清掃や清潔を保つことで在庫の品質を維持し、しつけによってこれらの活動を継続的におこなう文化を醸成します。
上流工程で在庫を持つ
在庫を上流工程で持つことにより、製造プロセス全体の効率向上が可能です。
例えば、製品の完成形に近い形での在庫ほど、在庫の使用用途が限られてしまいます。対して、上流工程で在庫を持てば、別の製品の部品として使用するといった使用用途を広げられます。
上流工程で在庫を持ちやすくする方法は、製品に使用する原材料の共通化です。1つの在庫の使用用途を増やすという考え方が重要です。
そうすることで、製品を在庫にすることなく、需要が急増して製造量を増やすといったイレギュラーにも対応できます。加えて、1つの部品の購入数が大幅に増加するため、部品単価の値下げ交渉も以前よりしやすくなります。
原料の状態で在庫にする
製品として完成する前の原料の状態で在庫を持つことにより、在庫量を減らせます。
製品ごとに原材料を買うと、製品ごとに在庫数を持たなくてはいけません。原材料自体をまとめて発注し、発注した原材料を製品ごとに分配すると在庫の個数の削減が可能です。
それだけでなく、製品に近い状態の在庫は保管スペースに広さを要しますが、原材料であれば、保管スペースは最小限にできます。
ただし、原材料を社内で加工するため、工数が増える点と端材が発生し廃棄がでる点には注意が必要です。
1回の購入数を減らす
1度に購入する数量を減らし、必要な分だけを小分けで購入すれば在庫を減らせます。保管スペースの節約や在庫管理の手間の削減も可能です。
最終的に購入する個数は同じでも、先にまとめて購入するか分けて購入するかで、その他にかかるコストが変動します。分けて買うことで余分なコストや在庫が余るリスクを回避しキャッシュフローの改善にもつながります。
また、製品の需要の変動にも柔軟に対応しやすくなり、無駄な在庫を抱えてしまうリスクも防止可能です。
発注点を決める
発注点の設定は、無駄のない発注が可能です。
発注点とは、商品の補充が必要となる在庫の最小数量です。発注点の設定は、最適なタイミングで必要な量を発注ができます。在庫切れを防ぎつつ、過剰在庫を避けられるため、重要な設定項目です。
発注点の設定には過去の販売データや需要予測を活用し、適切なタイミングを設定する必要があります。しばらく発注点の見直しをしてない場合は、直近の製品の需要予測といったデータを踏まえて、一度見直しをおすすめします。
製品数を減らす
製品のバリエーション自体を減らすのも在庫削減の方法です。売れていない製品の生産を中止したり、似たような商品を統合在庫の種類を減らしたりと、在庫管理工数のシンプル化に効果的です。
また、製造プロセスの効率化やコスト削減にもつながります。
適正在庫数を予測する
在庫削減を成功させるためには、適正在庫数を把握している必要があります。適正在庫数の予測には、需要予測や販売データの分析が不可欠です。
需要予測とは、市場で企業の製品がどれくらい売れるかをあらかじめ予測することを指します。需要予測の一般的な手法は、下記の表の通りです。
手法 | 説明 |
移動平均法 | 過去の売上の移動平均を計算し、予測をする方法。移動平均単価=(受入棚卸資産の評価額+在庫棚卸資産 |
指数平滑法 | 前期の実績と前期の予測を基に、今月の予測を求める方法。(今期の予測)=a×(前期の実績)+(1-a)×(前期の予測) |
需要予測には、Excelや在庫管理システムなどの需要予測システム、AIやIoTを使用します。手軽なのはExcelですが、在庫管理システムやAIを使用すると、より精度の高い予測が可能です。
在庫削減をするタイミング
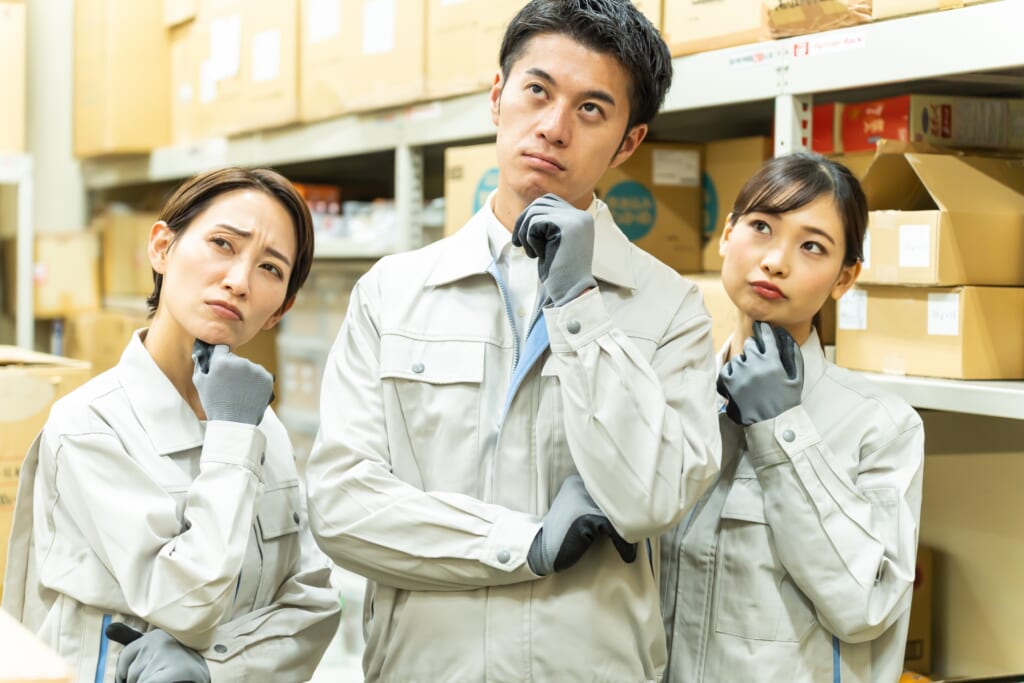
在庫削減を成功させるためには、在庫削減をおこなうタイミングを見極めることも重要です。在庫削減をおこなうべきタイミングを紹介します。参考にして、自社に取り入れてみてください。
コスト削減に迫られたとき
企業がコスト削減を迫られたときは、在庫削減を検討すべきタイミングです。在庫の保管には、倉庫の賃貸料や保管設備の維持、人件費などの多くのコストがかかります。これらのコストの削減で、企業の収益性の向上が可能です。
特に、経済状況が厳しい時期や業績が低迷している時期には、在庫削減で経営の安定化を図ることが重要です。
棚卸のタイミング
棚卸のタイミングも、在庫削減をおこなう良い機会です。棚卸は、在庫の現状を把握し、不要な在庫や過剰在庫を特定するための重要なプロセスです。
このタイミングで在庫を見直し、不要な在庫を削減、保管スペースの有効活用や在庫管理の効率化が図れます。
また、棚卸の結果を基に在庫管理システムを見直し、適切な在庫レベルを維持するための改善策を講じられます。
需要予測の更新時
需要予測の更新時も、在庫削減をおこなうタイミングとして適しています。需要予測は、将来の販売量を予測し、適切な在庫レベルを設定するための重要なツールです。
需要予測を更新すること、過去のデータや市場の変動を反映した最新の予測が得られます。この予測を基に在庫を見直し、過剰在庫や不足在庫を防ぐための調整が可能です。
特に、季節変動や新製品の発売など、需要が大きく変動するタイミングでは、需要予測の更新とともに在庫削減をすると効果的です。
在庫管理のDX促進で在庫削減の負担を軽減
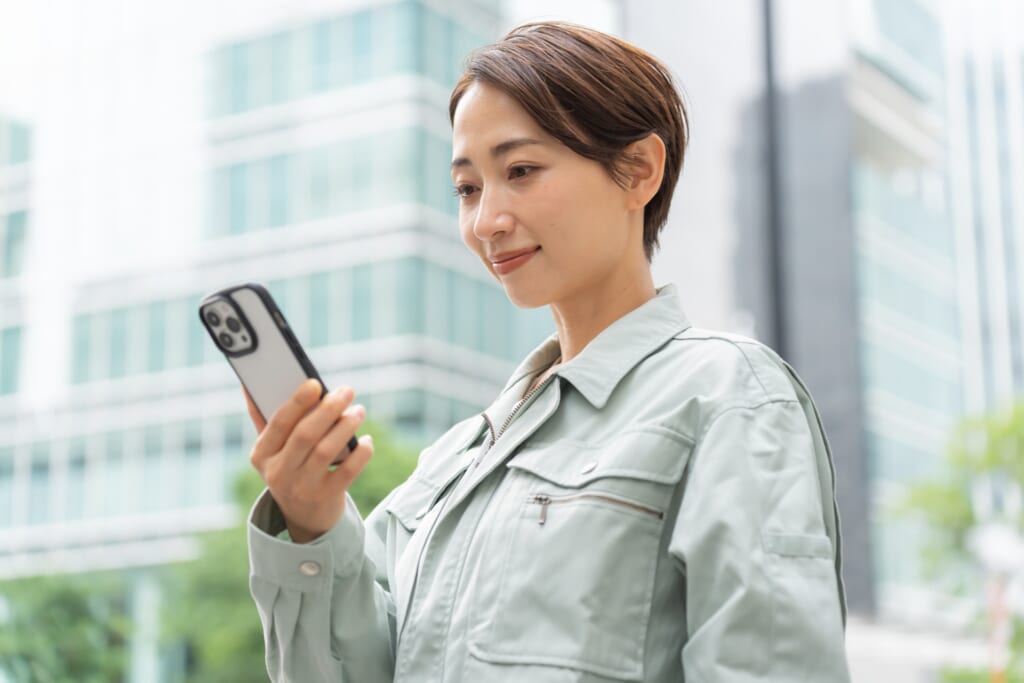
在庫削減は、在庫管理の一部です。そのため在庫管理自体の負担を減らせば、在庫削減もシンプルにできます。
在庫管理の負担軽減にはDX促進をオススメします。DX促進すればリアルタイムに在庫管理ができ、需要予測の精度の向上、自動発注システムの導入などが可能です。
また、管理をおこなう職員の負担の軽減にもつながるため、余分なコストを別の用途へ運用できるようにもなります。そうすることでより企業の持続可能な成長を可能にします。
株式会社サンソウシステムズでは、導入社数No.1(富士キメラ総研 2023年8月8日発刊)の現場帳票システム「i-Reporter」の導入を支援する『ちょこっと相談室』という無料のオンライン相談窓口を設けております。
現場帳票のシステム化を検討する際、「時間がなくて調査ができない」「導入しても運用できるか不安」「他社製品と比較してどうなのか」といった課題や不安がつきものです。
そのような企業様も安心してください。コンサルティング実績の多い弊社であれば、課題のヒアリングから業務効率化に向けた、目標設定・試験導入、その後の本導入から運用まで伴走支援いたします。
まず、やるべきことを整理するだけでもメリットになります。
お話を伺いたい方は、無料の『ちょこっと相談室』(Teams:オンライン)で、お気軽にご相談ください。現状課題のヒアリングから丁寧に対応させていただきます。